バーチャルツインでバッテリーの経年劣化解析
セル内の劣化プロセスは容量の減少を引き起こし、車両の航続距離を短くします。また、劣化はバッテリーの内部抵抗を増加させます。この内部抵抗は損失を増加させ、バッテリー内に追加の熱を生成します。
バッテリーの劣化には主に2つのタイプがあります:カレンダー劣化とサイクル劣化です。カレンダー劣化は、時間の経過とともに性能と容量が徐々に減少することを指します。このプロセスは、特にバッテリーの温度や充電状態などのさまざまな保管条件に影響されます。例えば、外部温度が高すぎたり低すぎたりすると、カレンダー劣化プロセスが加速します。
一方、サイクル劣化はバッテリーの使用方法、特に充電と放電のサイクルによって引き起こされます。充電プロセス中の動作条件は、バッテリーの寿命に大きな影響を与える可能性があります。
バッテリーの劣化に影響を与えるもう一つの重要な要素は、材料の選択です。異なる材料は、サイクル安定性やエネルギー密度に関して異なる特性を持っています。例えば、現在人気のあるLFPバッテリー(リチウムリン酸鉄)は、従来のNMCバッテリー(ニッケル-マンガン-コバルト)よりもサイクル安定性が高いですが、エネルギー密度は低いです。
バッテリーの主な劣化メカニズム
リチウムメッキは低温での充電中に発生する現象です。金属リチウムのデンドライトがアノードに形成され、イオン輸送を妨げます。これらのデンドライトは他の電極に向かって広がり、セパレーターを貫通して内部短絡を引き起こすこともあります。活性材料の損失は老化のもう一つの影響であり、材料が充電輸送に利用できなくなり、バッテリー内で「死んだ材料」となり、性能をさらに低下させます。
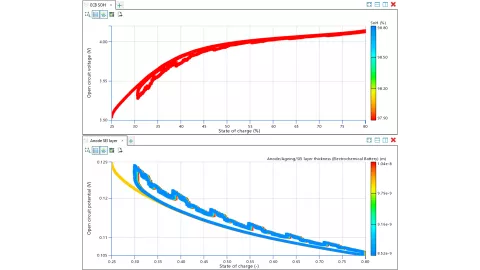
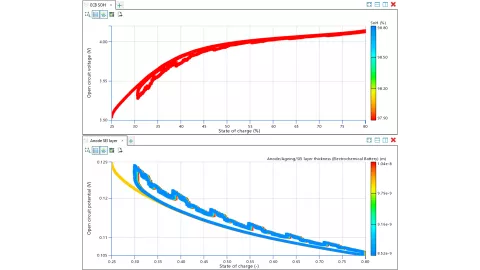
バッテリー劣化に関連する動作条件
動作条件はバッテリーの劣化において決定的な役割を果たし、その性能と寿命に大きな影響を与えます。
動作温度は、特に充電プロセス中にバッテリーの劣化に影響を与える重要な要素です。効率的な急速充電を確保するためには、充電プロセスの前にバッテリーがすでに理想的な温度範囲にあるか、適切に加熱または冷却されていることが非常に重要です。
もう一つの側面は充電容量です。高い充電容量は高電流を意味し、これが低温でバッテリーを劣化させる可能性があります。このため、低温ではゆっくりと開始し、バッテリーが温まるまで充電電力を調整することが推奨されます。
充放電サイクルもリチウムイオンバッテリーの寿命にとって非常に重要です。バッテリーの寿命が終わるまでに保証されるサイクル数がよく述べられます。サイクル劣化を減らすためには、最適な範囲でのみ充電し、充電ウィンドウを20%から80%の範囲に移動することが推奨されます。放電深度が低いとサイクル安定性が指数関数的に向上します。その結果、バッテリーへの負荷が少なくなり、ガス生成や電解質の損失などの非可逆的な化学プロセスによる劣化反応が引き起こされません。
これらの動作条件を考慮することは、性能と寿命が向上したバッテリーの開発にとって非常に重要です。このため、シミュレーションモデルを使用して、バッテリー劣化に対するさまざまな動作条件の影響を予測し、効率的な運用戦略の開発をサポートすることができます。
バッテリー劣化の予測は、効率的で長寿命なバッテリーシステムの開発に不可欠です。シミュレーションモデルは、さまざまな動作条件が劣化プロセスに与える影響を予測し、対応する最適化戦略を開発する上で中心的な役割を果たします。
AVLは、最小限の労力で長期シミュレーションを実行できる電気化学モデルを提供しています。これらのシミュレーションモデルは、従来のテストベンチでの物理的試験では不可能なバッテリーの内部状態を推定および計算することができます。
テストベンチでは測定できないが、シミュレーションで計算できるアノード電位は、バッテリー劣化の重要な指標です。セル劣化のシミュレーションにより、充電曲線を最適化し、例えば急速充電中にリチウムメッキなどの劣化プロセスを回避するために、電力を限界に近づけることができますが、限界を超えないようにします。
充電および放電戦略をシミュレーションし、検証された劣化モデルに充電プロファイルを適応させることで、サイクル安定性に関する質問に長期間にわたって回答することができます。これにより、ユーザーは数年間の運用期間をシミュレーションし、バッテリーの寿命について根拠のある声明を出すことができます。
劣化モデルのパラメータ化は、劣化したセルのデータに基づいており、実際のセルの劣化曲線との比較によって検証されます。曲線間に無視できるほどの偏差しか検出されない場合、テストベンチをオフにしてシミュレーションを独立して実行し続けることができます。シミュレーションモデルをテストベンチから切り離した後、約6か月の実時間を1か月でシミュレーションすることができ(ハードウェアによる)、大幅な時間とコストの節約が可能になります。
バッテリー開発プロセスにおけるシミュレーションの重要性の高まりは、バッテリーの最適な材料を探求する継続的な取り組みと密接に関連しています。LFP(リチウムリン酸鉄)などの材料は、従来のセル化学に比べてサイクル安定性と安全性が高く、寿命が長いため、ますます人気が高まっています。同時に、シミュレーションツールは絶えず進化しており、材料選択と劣化プロセスの影響をマッピングおよびパラメータ化する能力が向上しています。
従来のテストベンチシステムは依然として重要な役割を果たしていますが、シミュレーション技術の統合により、時間と費用を節約し、市場投入までの時間を短縮する機会が提供されます。テストベンチの使用とソフトウェアインザループシステムを組み合わせることで、バッテリー開発者はより情報に基づいた意思決定を行い、バッテリーシステムの性能を最適化することができます。これにより、市場投入までの時間が短縮され、より持続可能な未来のためのバッテリー技術の継続的な開発が支援されます。
最新の情報をお見逃しなく
シミュレーションのブログシリーズをご覧ください。今すぐ登録して最新情報を受け取りましょう。
テーマについてさらに詳しく知る
最新の情報をお見逃しなく
シミュレーションのブログシリーズをご覧ください。今すぐ登録して最新情報を受け取りましょう。