Entwicklung und Bewertung von Festoxidelektrolyseursystemen durch Simulation
- Blog
Globale Initiativen und Maßnahmen zur Erreichung langfristiger Klimaziele führen zur Entwicklung und Industrialisierung neuer Elektrolyseursysteme. Jedes Jahr wird ein deutliches Wachstum der angekündigten Elektrolyseur-Projekte vorhergesagt, und der Festoxid-Elektrolyseur (SOEC) ist eine der vielversprechendsten Technologien, da er die höchste Effizienz bietet. Andererseits hat die SOEC im Vergleich zu anderen Technologien einen geringeren Reifegrad, was die AVL dazu veranlasst hat, sich auf die Entwicklung, Integration und Optimierung von SOEC-Systemen zu konzentrieren. Der Stack steht immer im Mittelpunkt der SOEC-Entwicklung, während die Anlagenbilanz (BoP) so ausgelegt ist, dass sie die Stack-Anforderungen erfüllt und andere Attribute wie den angestrebten Systemwirkungsgrad erreicht. Die optimale Auslegung von Festoxidzellensystemen (SOC) mit BoP ist aufgrund der Systemkomplexität und der Zeitskalen der transienten Laständerungen eine sehr anspruchsvolle und kostspielige Aufgabe. Indem die Simulation in den Mittelpunkt des Entwurfsprozesses gestellt wird, ist die AVL in der Lage, das System mit einer geringeren Anzahl von Prototypen und einer kürzeren Prüfstandszeit zu optimieren. Virtuelle Zwillinge werden in der Entwurfsphase verwendet, um die Systemarchitektur für den besten Kompromiss zwischen Systemeffizienz und Systemkosten zu definieren, wobei alle relevanten Einschränkungen im Stack und Systembetrieb berücksichtigt werden. Die Wiederverwendung bestehender Simulationsmodelle während des gesamten Entwicklungsprozesses ist von entscheidender Bedeutung, da mehrere aufeinander folgende Aufgaben in der virtuellen Umgebung durchgeführt werden. Nach ersten Konzeptstudien verlagert sich der Schwerpunkt auf den Systembetrieb, der in der Entwicklung und Kalibrierung der Systemsteuerungsfunktionen gipfelt.
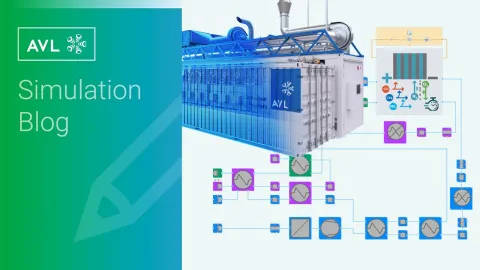
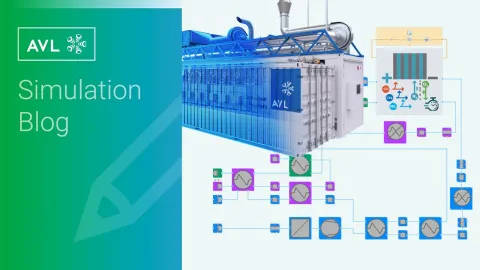
Die Entwicklung komplexer Systeme wie eines SOEC-Systems ist eine große Herausforderung, nicht nur, weil es sich um eine relativ neue Technologie handelt, sondern auch wegen anderer Aspekte wie Hochtemperaturbetrieb und sehr begrenzten Temperaturgradienten, die im Stack zulässig sind. Dies war einer der Hauptgründe für den Einsatz von AVL CRUISE™ M, einer multidisziplinären Systemsimulationssoftware, im Zentrum der Entwicklung. Die Software ermöglicht eine detaillierte elektrochemische Modellierung des Stacks und eine thermodynamische Modellierung des BoP-Systems, einschließlich Druckabfall, Wärmeübertragung, chemische und Dampf/Flüssigkeits-Gleichgewichtsberechnungen, die alle in 1D-Diskretisierung ausgewertet werden.
Beispiele für SOC-Stack und -Systemvalidierung
Ein wichtiger Teil der Softwareentwicklung ist ihre Validierung. Die nativen CRUISE M Stack- und BoP-Komponenten wurden anhand von Messungen aus der Literatur und/oder internen AVL-Projekten validiert. Die Abbildung unten zeigt validierte Stack-Beispiele, die sich entweder auf (a) den SOFC-Betrieb mit verschiedenen Brenngasmischungen aus H2, H2O, CO und CO2 oder (b) den Übergang zum reversiblen SOC-Betrieb (rSOC) konzentrieren. Die Ergebnisse der Polarisationskurven zeigen eine gute Übereinstimmung zwischen Messungen und Simulation. Geringfügige Abweichungen ergaben sich aufgrund von Unsicherheiten bei der Zell- und Stack-Geometrie, dem Alterungszustand und den Betriebsbedingungen, unter denen die Experimente durchgeführt wurden.


Die folgende Abbildung zeigt (a) ein validiertes SOFC-Stack-Beispiel, das in ein BoP-System integriert ist. Das System wird mit CH4 befeuert, das in einem externen Reformer und intern im Stack verarbeitet wird. Ein Teil des Abgasbrennstoffs wird rezirkuliert, um den Wirkungsgrad des Systems zu erhöhen, und der andere Teil wird in einem Nachbrenner oxidiert, um Schadstoffe zu reduzieren und die Wärme des Systems wieder zu nutzen. Aus den Ergebnissen ist ersichtlich, dass das Simulationsmodell das Verhalten eines bei AVL gebauten realen Systems genau abbildet, da alle wichtigen physikalischen Größen innerhalb definierter Qualitätsgrenzen lagen. Die Simulationsergebnisse (rote Kurven) werden anhand von Referenzdaten (schwarze Kurven) validiert und sind für (b) Luftelektrodendruck, (c) Abgastemperatur, (d) Reformer-Katalysatoreintrittstemperatur, (e) Brennstoffelektrodendruck, (f) Luftmassenstrom und (g) Systemleistung dargestellt.
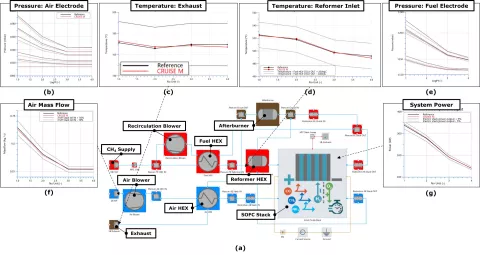
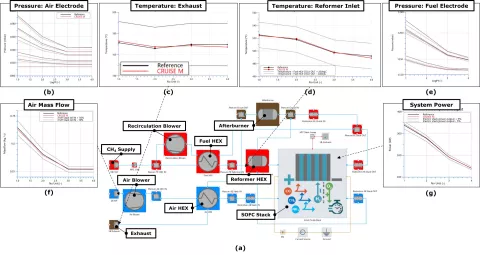
Ein 1D-Co-SOEC-Systemmodell für die Synthesegaserzeugung wurde entwickelt, um die Stack- und Systemleistung innerhalb verschiedener Systemdesignparameter zu analysieren.
Modellbeschreibung
In der Abbildung unten sehen Sie die Architektur des Co-SOEC-Systems. Es handelt sich um ein 100-kW-Elektrolyseursystem mit einem Verhältnis von Dampf zu Kohlenstoff von 2,5 und einer Brennstoffausnutzung und Rezirkulationsrate von etwa 75%. Der Stack arbeitet zwischen 770 °C und 850 °C, und das System erreicht unter Berücksichtigung des niedrigeren Heizwerts von Wasserstoff einen Wirkungsgrad von etwa 87,5%.
Der Luftelektrodenweg beginnt mit einem Filter und einem Kompressor (1), der die Luft zunächst durch Wärmetauscher (2) durch das System drückt, wo sie sich auf das gewünschte Temperaturniveau erwärmt. Die erwärmte Luft tritt in den Stack (3) ein, wo durch den Elektrolyseprozess Sauerstoff gebildet wird. Am Ausgang des Stacks erfolgt die erste Sequenz der Abgaseinspritzung und des Oxidationskatalysators (4), der die Luft erwärmt und sie über den Brennstoffwärmetauscher (5) weiter an die Brennstoffelektrode überträgt. Es folgt die zweite Sequenz von Abgaseinspritzung und Oxidationskatalysator (6), die die Luftelektrodenseite über Luftwärmetauscher (7) aufheizt. Ein Teil der Prozesswärme wird an den Luftstrom übertragen, der andere Teil über Wärmetauscher an den Dampf und das CO2 (8). Am Ende, bevor die Luft das System verlässt, regelt ein Drosselventil (9) den Gegendruck, um die gewünschte Druckdifferenz zwischen Luft und Brennstoffelektrode sicherzustellen.
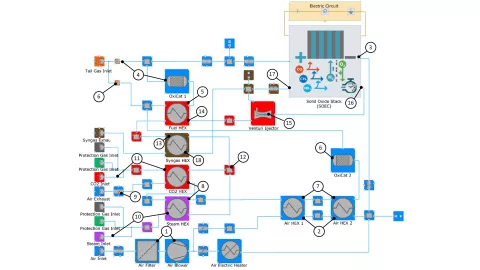
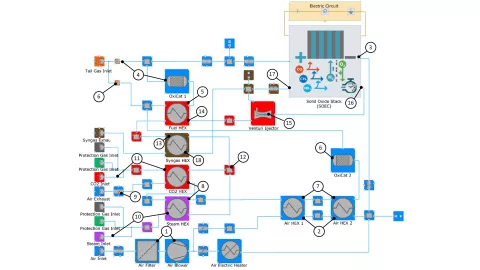
Der Weg der Brennstoffelektrode beginnt mit der getrennten Zufuhr von Dampf (10) und CO2 (11) mit entsprechendem Wärmetauscher, bevor sich die Gase vermischen (12) und den Weg zum Synthesegaswärmetauscher (13) nehmen. Der Weg setzt sich im Brennstoffwärmetauscher (14) fort, wo die genaue Temperatur geregelt wird. Der gemischte Dampf und das CO2 werden unter hohem Druck in den Venturi-Injektor (15) eingespritzt, wo eine beträchtliche Menge des Synthesegases in den Rezirkulationskreislauf und direkt in den Kamineinlass (16) zurückgezogen wird, was eine höhere Reinheit des Synthesegases am Kaminauslass (17) gewährleistet. Das Synthesegas wird im Wärmetauscher (18) leicht abgekühlt, wodurch etwas Wärme in das System zurückgeführt wird.
Neben der Systemarchitektur und der Auswahl der Komponenten gibt es auch mehrere Aktoren, die für ein effizientes System richtig gesteuert werden müssen.
Die Systemkontrollen in dem vorgestellten Modell sind:
- Massenstrom der Abgaseinspritzung 1: Zum Aufheizen der Brennstoffelektrode auf die angestrebte Eintrittstemperatur.
- Massenstrom der Abgaseinspritzung 2: Zum Aufheizen der Luftelektrode auf die Zieleintrittstemperatur.
- Geschwindigkeit des Luftgebläses: Steuerung der Temperaturdifferenz des Schornsteins auf einen akzeptablen Temperaturbereich und eine niedrigere O2-Grenze in der Luftelektrode.
- Elektrischer Strom durch den Schornstein: Dient zur Steuerung der Belastung des Systems.
- Kraftstoff-Abgasrückführungsventil: Dient dazu, die gewünschte Rezirkulationsrate zu erreichen, um die angestrebte Synthesegaszusammensetzung zu erreichen und gleichzeitig ein Verhungern des Brennstoffs zu verhindern.
- Gegendruckventil: Zur Regulierung der Druckdifferenz zwischen den beiden Elektroden.
- Dampf- und CO2-Massenströme: Sollten in den richtigen Verhältnissen reguliert werden, um das richtige Verhältnis von Dampf zu Kohlenstoff zu erreichen und das System auf den erforderlichen Auslastungen (Stöchiometrien) zu halten.
Das thermodynamische Modell wurde auf der Grundlage der Datenblätter der Zulieferer für Luftgebläse, Wärmetauscher, Venturi-Injektor und Stack-Komponenten parametrisiert. Die Steuerungen wurden für den Basisbetrieb entwickelt, um die Leistung der Systemarchitektur und ihr Verhalten bei unterschiedlichen Umgebungs- und Betriebsbedingungen zu bewerten, was die Untersuchung von Konstruktionsänderungen, Systemoptimierung und Kompromissen zwischen Systemkosten und Effizienz ermöglicht. Das Modell kann auch für die Entwicklung detaillierter Steuerfunktionen und deren Kalibrierung verwendet werden.
Anwendungsfälle von Simulationsmodellen im V-Prozess
Die folgende Abbildung veranschaulicht die Simulationsmöglichkeiten von CRUISE M in einem typischen V-Prozess, von denen einige bereits in unserem SOEC-Webinar und im SOFC-Webinar vorgestellt wurden.
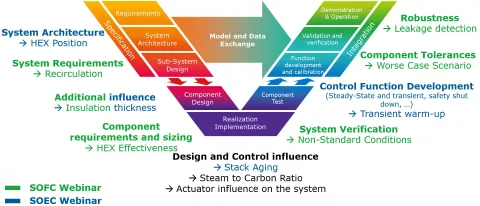
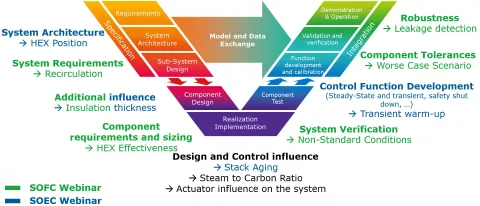
Hier können Sie auf die kostenlosen On-Demand-Webinare zugreifen:
SOFC
SOEL
In den folgenden Abschnitten werden einige der Anwendungsfälle des thermodynamischen Modells und der Steuerungen beschrieben, einschließlich der Ergebnisse und Beobachtungen von Fallstudien.
Architektur-Varianten
Die Systemarchitektur bestimmt in hohem Maße die Anwendung und Effizienz des gewünschten Systems. Die Abbildung unten zeigt (a), (b) den Vergleich zwischen zwei Varianten der Co-SOEC-Systemarchitektur. Die ursprüngliche Architektur entspricht der oben vorgestellten Co-SOEC-Architektur, die um einen zusätzlichen Wärmetauscher auf der Luftelektrodenseite erweitert wurde (rot umrandete Anschlüsse). Die Ergebnisse (c) zeigen, dass ein zusätzlicher, an der richtigen Stelle integrierter Wärmetauscher sehr vorteilhaft sein kann, da er die Abgastemperatur und die Enthalpieverluste reduziert, was zu einer attraktiven Steigerung der Systemeffizienz führt. Er kann zusätzliche Vorteile bringen, indem er die maximale Systemtemperatur senkt und eine potenzielle Systemverbesserung durch Syngas-Wärmerückgewinnung ermöglicht. Mit zunehmender Größe des Systems können sich jedoch auch Nachteile ergeben, wie höhere Druckverluste und Wärmeverluste.
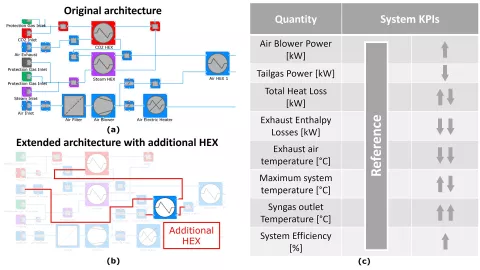
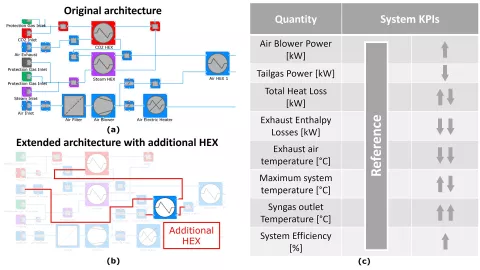
System-Isolierung
Die während des Systembetriebs auftretenden Wärmeverluste stehen in engem Zusammenhang mit der Isolierung der Komponenten, die z. B. bei einem Co-SOEC-System durch den Abgasbrennstoff kompensiert werden muss, was sich direkt auf den Gesamtwirkungsgrad des Systems auswirkt. Zumindest eine dünne Isolierschicht ist erforderlich, um den Stack innerhalb der erforderlichen Temperaturtoleranz zu halten. Es besteht jedoch immer ein Kompromiss zwischen den Systemkosten (in Bezug auf die Isolierungsdicke) und der Systemeffizienz, wie in der nachstehenden Abbildung dargestellt.
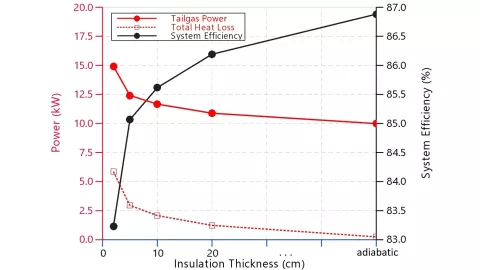
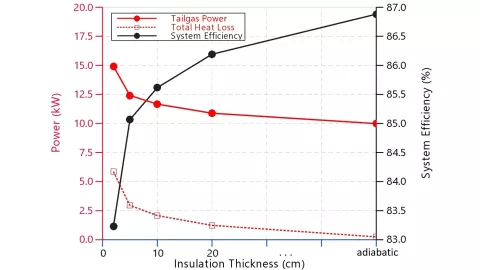
Auswahl von Luftgebläsen
Die Auswahl von Komponenten ist eine der typischsten Aufgaben der Systemsimulation. Wenn man sich für hocheffiziente und teure Komponenten entscheidet, ist es sinnvoll zu untersuchen, ob sich der Aufwand für die erbrachte Leistung lohnt. Die Effizienz der Gebläse hat einen direkten und indirekten Einfluss auf die Systemeffizienz. Niedrigere Wirkungsgrade führen zu höheren Gebläse-Austrittstemperaturen. Dies hat zwei Auswirkungen: Erstens wird die erforderliche Leistung des Abgases reduziert, und zweitens verhindert die höhere Temperatur auf der kalten Seite des Wärmetauschers eine effiziente Rückgewinnung der heißen Gase, was zu höheren Abgas-Enthalpieverlusten führt. Etwa 10% Unterschied im Wirkungsgrad des Gebläses führen zu einem Systemwirkungsgrad von 0,1%, wie in der nachstehenden Abbildung dargestellt.
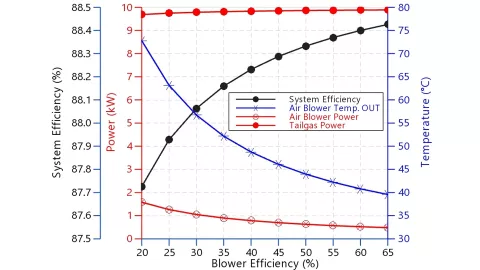
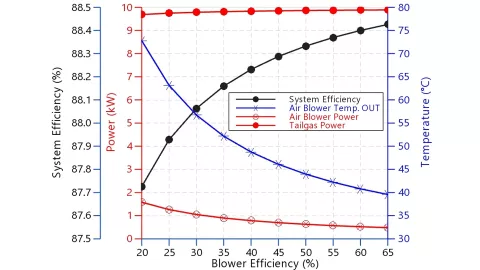
Dampf-Kohlenstoff-Verhältnis
Das Dampf-Kohlenstoff-Verhältnis in einem typischen Co-SOEC-System wird im Voraus festgelegt, um die Anforderungen anderer Prozesse zu erfüllen, z. B. die Zielbrennstoffproduktion bei der Fischer-Tropsch-Synthese. Neben der Gaszusammensetzung hat das Dampf-Kohlenstoff-Verhältnis auch noch andere, geringere Einflüsse auf die Systemleistung. Wie in der nachstehenden Abbildung zu sehen ist, ist die Zellenspannung im Allgemeinen leicht unterschiedlich, was zu einer geringeren erforderlichen elektrischen Leistung führt, die die gleiche Verringerung der Synthesegasleistung bewirkt, während andere Leistungen gleich bleiben (Gebläseleistung, Wärmeverluste, Enthalpieverluste), was zu unterschiedlichen Systemwirkungsgraden führt.
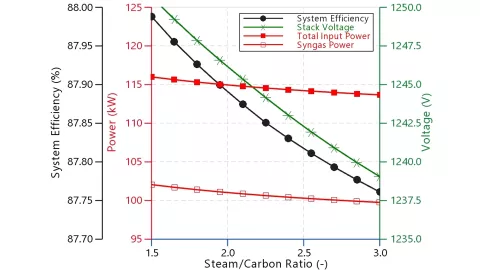
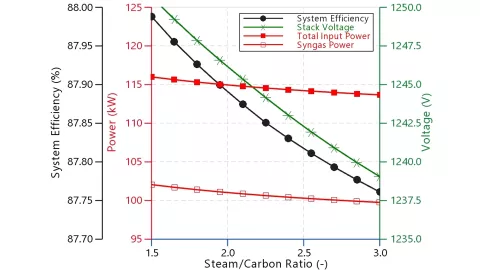
Brennstoff-Abgasrückführungsrate
Die Abgasrückführungsrate ist eine Gegenmaßnahme zur Erfüllung der Systemanforderungen hinsichtlich der Synthesegaszusammensetzung. Die folgende Abbildung zeigt, dass (b) die Reinheit des erzeugten Synthesegases (H2- und CO-Konzentration) umso höher ist, je höher die Rezirkulationsrate ist, wobei der Grenzwert für die Brennstoffausnutzung im Schornstein dennoch eingehalten wird. Die Rezirkulationsrate hat noch weitere positive Auswirkungen, z. B. (a) verringert sie den Temperaturgradienten über dem Kamin, was zur Kontrolle des BoP beiträgt. Andererseits erhöht sie die Zellspannung, was zu einem höheren Strombedarf für die Elektrolyse führt. Im endothermen Stackbetrieb hat dies keinen Einfluss auf die Systemeffizienz, da für ähnliche Temperaturzustände einfach weniger Abgas benötigt wird.
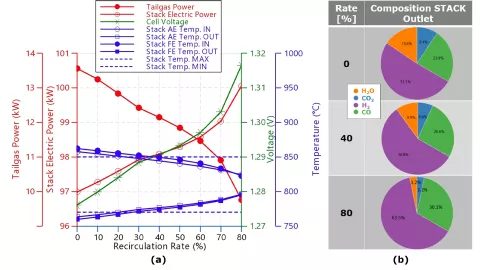
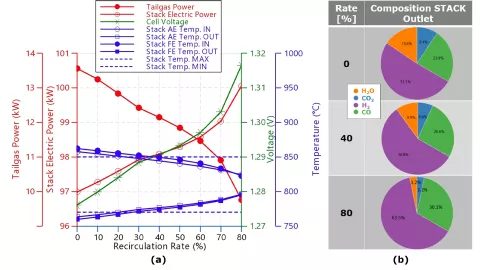
Stack-Alterung
Mit zunehmendem Alter des Schornsteins nimmt seine Leistung ab, was zu einem Anstieg der erforderlichen Spannung für den gleichen Betrieb führt, was auch ein anderes Temperaturprofil im Schornstein zur Folge hat. Der Systemwirkungsgrad nimmt mit zunehmendem Alter nicht unbedingt ab, da Schornsteine endotherm sind und zusätzliche Wärme im System genutzt wird, unabhängig davon, ob sie aus dem Schornstein oder aus anderen Quellen (Abgaseinspritzung) stammt. Die Hauptaufgabe bei der Auslegung der Alterung besteht darin, das System so zu steuern, dass der Schornstein innerhalb der erforderlichen Temperaturtoleranzen gehalten wird, in dieser Analyse zwischen 770 °C und 850 °C. Dies kann entweder durch die Gebläsedrehzahl oder/und den Betrieb mit elektrischem Strom erreicht werden.
Die Steuerung des Stroms und der Gebläsedrehzahl bei unterschiedlichen Alterungsfaktoren (die Alterung wird als linear skalierter Spannungsanstieg modelliert) wirkt sich auf die Temperaturprofile im Stapel aus, wie in der Abbildung unten zu sehen ist. Eine Beobachtung ist, dass es bei kleineren Alterungsfaktoren (bis zu 6%) möglich ist, Temperaturtoleranzen mit einer einzigen Regelungsänderung zu erreichen, während bei höheren Alterungsfaktoren beide Maßnahmen gleichzeitig angewendet werden sollten.
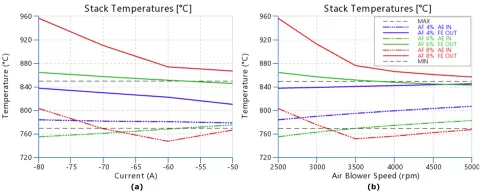
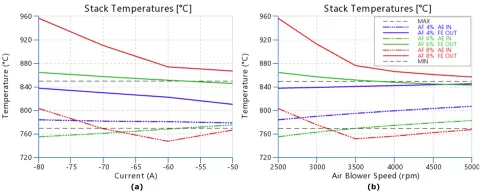
Zu diesem Zweck wurde eine Versuchsplanung (DOE) durchgeführt, bei der die Gebläsedrehzahl (zwischen 3000 U/min und 6000 U/min) und der Strom (zwischen -80 A und -55 A) für einen Alterungsfaktor von 10% (10% Spannungserhöhung im Vergleich zum frischen Stackbetrieb) variiert wurden. Die Stack-Temperaturen an den Ein- und Auslässen der beiden Elektroden sind in der folgenden Abbildung dargestellt (a), (b), (c), (d). Die schwarzen Punkte stellen die Auslegungspunkte dar, und der Temperaturbalken ist so definiert, dass er Temperaturen oberhalb des Maximums von 850 °C (rot), unterhalb des Minimums von 770 °C (blau) und im akzeptablen Bereich (grün) anzeigt. Es ist festzustellen, dass (d) die Auslasstemperatur der Brennelektrode am kritischsten war, da sie die geringste Anzahl der möglichen optimalen Betriebspunkte (6 Punkte) abdeckte, und (e) der Betriebspunkt mit einer Gebläsedrehzahl von 5000 U/min und einem Strom von -55 A den höchsten Systemwirkungsgrad von 80% ergab.
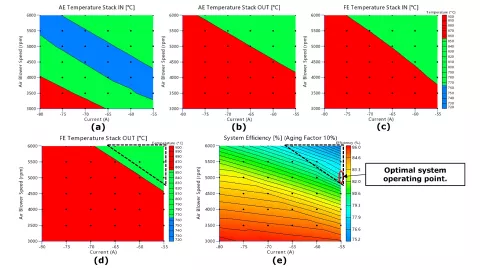
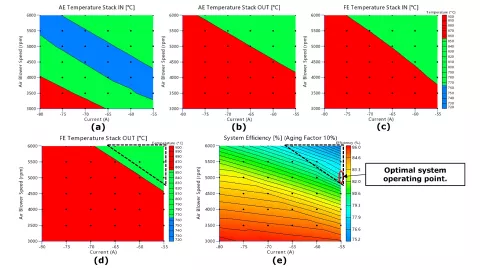
Mit einer kombinierten Stromreduzierung und einer Erhöhung der Gebläsedrehzahl ist es möglich, einen plausiblen Betrieb für einen Schornsteinalterungsfaktor von 10% zu erreichen. Der Benutzer kann von DOE oder Optimierung profitieren, um die Kontrollstrategie zu übernehmen.
Leckagen in der Luftzufuhr
Leckagen im System können aufgrund verschiedener Betriebsfaktoren auftreten und beeinflussen die Systemeffizienz, da ein Teil des erwärmten Gases verloren geht. Dieser Verlust muss durch eine zusätzliche Energiequelle, wie z. B. eine Abgaseinspeisung, kompensiert werden. Idealerweise müssen Leckagen auf irgendeine Weise von der Steuereinheit erkannt werden, und Simulationsmodelle können zur Entwicklung und Kalibrierung von Diagnosen für die Leckageerkennung verwendet werden. Es liegt auf der Hand, dass sich der Massendurchfluss aufgrund von Leckagen verringert, was zwei Auswirkungen hat, die in der nachstehenden Abbildung dargestellt sind: einen Anstieg der Abgastemperatur (da mehr Abgasenergie in einen geringeren Massendurchfluss umgesetzt wird) und eine niedrigere Temperatur der Eintrittsgase (da weniger Wärme von den Abgasen auf die Eintrittsgase übertragen werden kann). Dieser Unterschied zwischen den beiden Temperaturen könnte ein gutes Indiz dafür sein, dass es im System zu Leckagen kommt.
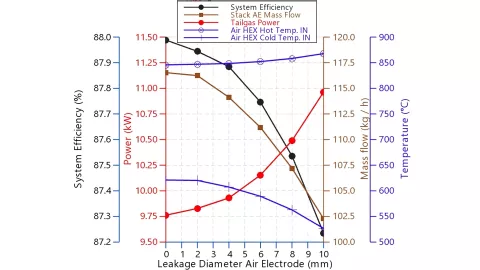
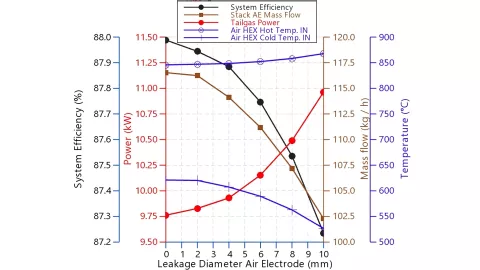
Entwicklung von Steuerfunktionen
Die Verwendung einer virtuellen Umgebung für die Entwicklung von Steuerfunktionen und die Kalibrierung von Steuergeräten ist ein entscheidender Schritt, um die Aktivitäten in der Entwicklungsphase zu beschleunigen, kostspielige Tests auf dem Prüfstand zu reduzieren und vor allem Schäden am eigentlichen System zu vermeiden. Ursprünglich wurden grundlegende Steuerungen für den stationären Betrieb entwickelt. Die Entwicklung einer instationären Systemsteuerung, einschließlich der Aufwärmphase, ist aufgrund der langfristigen Natur des Prozesses besonders anspruchsvoll. Die wichtigste davon ist die Begrenzung des Temperaturgradienten im Schornstein, die zu einer Aufwärmzeit von bis zu 10 Stunden führt. Die Simulation spielt eine sehr wichtige Rolle, da sie schneller ist als die Echtzeit und eine Verringerung der thermischen Trägheit ermöglicht, so dass die Simulation von einem 10-stündigen Prozess auf weniger als 20 Minuten reduziert werden kann, wie in der Abbildung unten dargestellt.
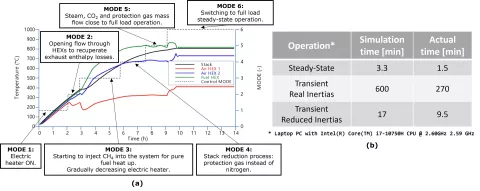
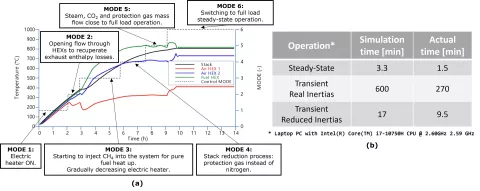
Im letzten Jahr gab es eine starke Motivation, die Modellierung komplexer Systeme auch Ingenieuren zugänglich zu machen, die mit dem Thema noch nicht vertraut sind, und Experten in kürzester Zeit etwas Nützliches an die Hand zu geben. Unsere SOEC-Systeme können mit dem SOEC-Generator aufgebaut werden, der automatisch ein Modell mit allen BOP-Komponenten rund um den Stack erstellt. Das System wird entsprechend den Informationen über die aktive Zellfläche und die Anzahl der Zellen dimensioniert und bietet auch eine automatische Manipulation der Modellierungsparameter, um unterschiedliche Isolierungs- und Wärmetauschereffektivität zu berücksichtigen. Außerdem bietet es vordefinierte Simulations-Dashboards mit allen wichtigen Leistungsindikatoren (KPIs) und thermodynamischen Größen (Massenströme, Drücke, Temperaturen, Zusammensetzung) zur sofortigen Modellbewertung.
Die Simulationsmethodik und die multidisziplinäre 1D-Systemsimulationssoftware CRUISE M wurden entwickelt und anhand von Messungen der realen Anwendungsfälle validiert. Der Festoxidstapel und der Gaspfad zeichnen sich durch einen echtzeitfähigen, domänen- und skalenübergreifenden Modellierungsansatz aus, der alle thermodynamischen, chemischen und elektrochemischen Prozesse berücksichtigt und zusammen mit DoE- und Optimierungsfunktionen eine leistungsstarke Kombination für eine umfassende Systemsimulation darstellt. In der vorgestellten Simulationsstudie wurde dies durch die Auflistung mehrerer Anwendungsfälle demonstriert, beginnend mit Konzeptentscheidungen (d.h. Systemarchitektur, Isolierung, Komponentenauswahl), weiterführend mit Betriebsstrategien (d.h. Abgasrückführungsrate, Stackalterung, Dampf-Kohlenstoff-Verhältnis) und endend mit der Entwicklung von Kontrollfunktionen (d.h. für Leckageerkennung und transientes Aufwärmen). Vor allem die letztgenannten Aufgaben bieten das größte Potenzial für erhebliche Kosteneinsparungen, indem teure Tests auf dem Prüfstand durch virtuelle Zwillinge ersetzt werden.
Verpassen Sie keinen Simulations Blog
Melden Sie sich noch heute an und bleiben Sie informiert!
Gefällt Ihnen das? Vielleicht gefallen Ihnen auch diese...
Lorem ipsum dolor sit amet, consectetur adipiscing elit. Pellentesque sit non integer
commodo turpis amet nibh. Lorem ipsum dolor sit amet.
Lorem ipsum dolor sit amet, consectetur adipiscing elit. Pellentesque sit non integer
commodo turpis amet nibh. Lorem ipsum dolor sit amet.
Lorem ipsum dolor sit amet, consectetur adipiscing elit. Pellentesque sit non integer
commodo turpis amet nibh. Lorem ipsum dolor sit amet.
Lorem ipsum dolor sit amet, consectetur adipiscing elit. Pellentesque sit non integer
commodo turpis amet nibh. Lorem ipsum dolor sit amet.
Mehr zu Thema
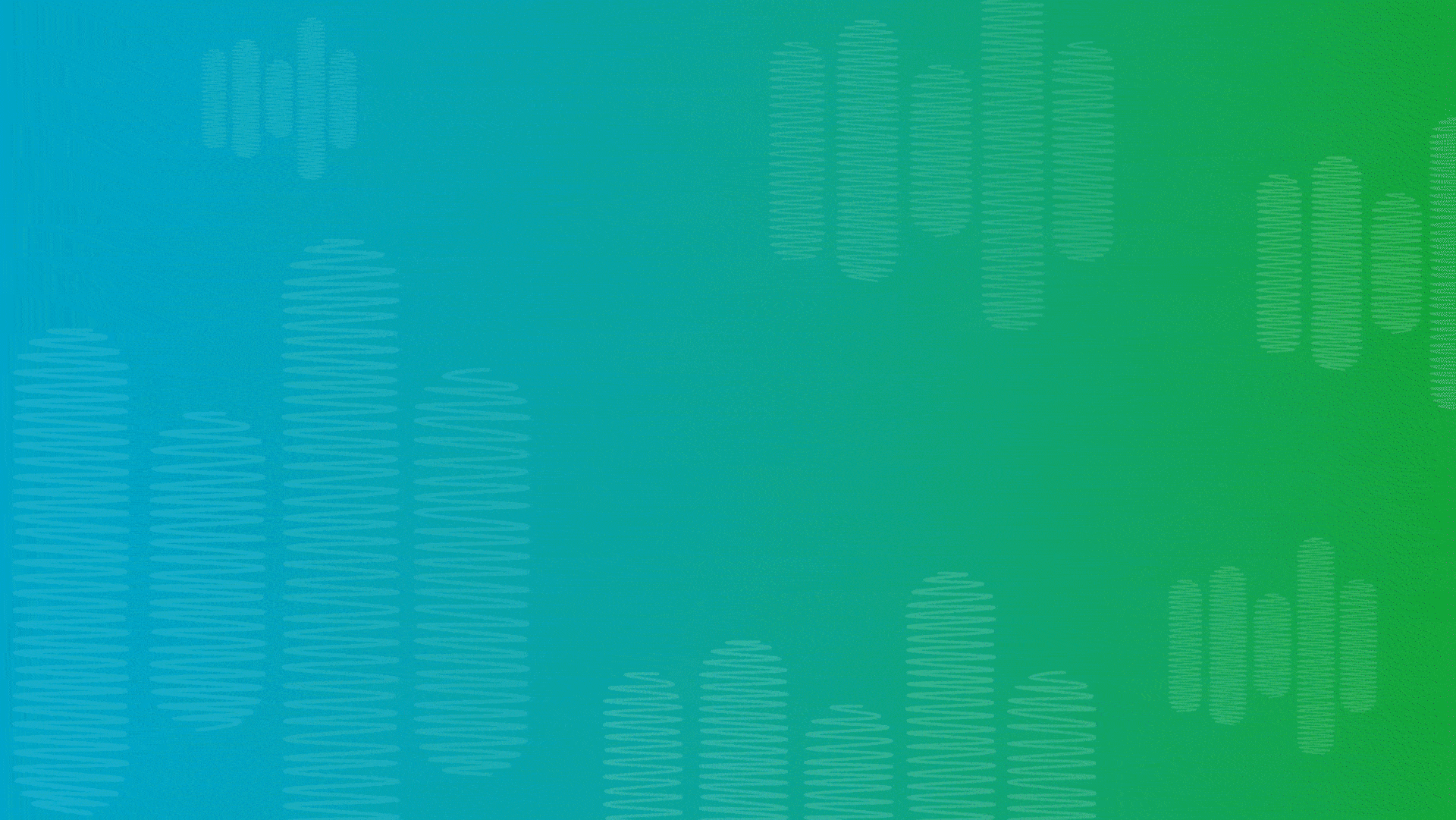
Elektrolyseure – das Herzstück der grünen Wasserstoffproduktion – stehen derzeit im Mittelpunkt intensiver Forschungs- und Innovationsaktivitäten mit dem Ziel, die Effizienz zu steigern, den Leistungsverlust infolge von Degradation zu minimieren, den Entwicklungsaufwand zu verringern sowie die Markteinführung zu beschleunigen.
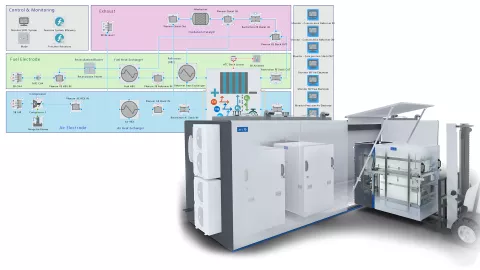
Festoxid-Brennstoffzellen (SOFC) sind eine vielversprechende Technologie für die Stromerzeugung im Rahmen von Systemen für erneuerbare Energien. Dies ist vor allem auf ihren hohen Wirkungsgrad, ihre Brennstoffflexibilität und ihre Umweltverträglichkeit zurückzuführen.
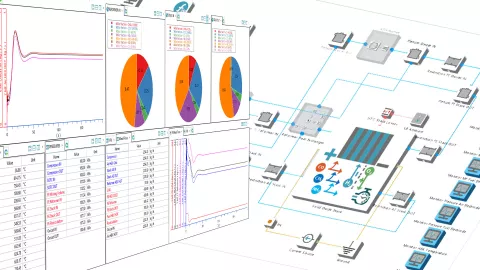
Mit dem Ziel einer drastischen CO₂-Reduzierung in Industrie und Mobilität steht die Welt derzeit vor der Herausforderung, grünen Wasserstoff zu erschwinglichen Preisen und in ausreichenden Mengen zu produzieren.
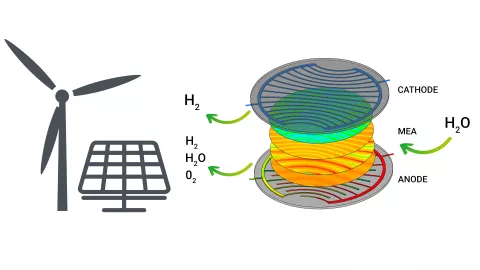
Wasserstoff speichert Überschussenergie aus erneuerbaren Quellen effektiv. PEM-Elektrolyseure dominieren hier dank ihrer Effizienz und Leistung. Unsere 3D-Multiphysik-Simulation ermöglicht detaillierte Einblicke für die Optimierung von Elektrolyseuren und Materialauswahl und mehr dazu können Sie in unserem Webinar entdecken.
Verpassen Sie keinen Simulations Blog
Melden Sie sich noch heute an und bleiben Sie informiert!