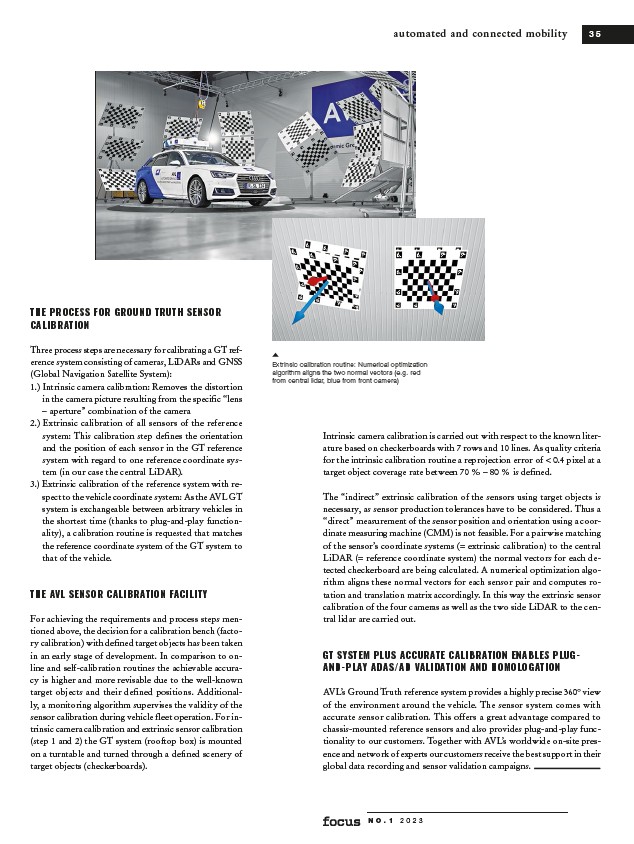
automated and connected mobility 3 5
Extrinsic calibration routine: Numerical optimization
algorithm aligns the two normal vectors (e.g. red
from central lidar, blue from front camera)
N O . 1 2 0 2 3
THE PROCESS FOR GROUND TRUTH SENSOR
CALIBRATION
Three process steps are necessary for calibrating a GT reference
system consisting of cameras, LiDARs and GNSS
(Global Navigation Satellite System):
1.) Intrinsic camera calibration: Removes the distortion
in the camera picture resulting from the specific “lens
– aperture” combination of the camera
2.) Extrinsic calibration of all sensors of the reference
system: This calibration step defines the orientation
and the position of each sensor in the GT reference
system with regard to one reference coordinate system
(in our case the central LiDAR).
3.) Extrinsic calibration of the reference system with respect
to the vehicle coordinate system: As the AVL GT
system is exchangeable between arbitrary vehicles in
the shortest time (thanks to plug-and-play functionality),
a calibration routine is requested that matches
the reference coordinate system of the GT system to
that of the vehicle.
THE AVL SENSOR CALIBRATION FACILITY
For achieving the requirements and process steps mentioned
above, the decision for a calibration bench (factory
calibration) with defined target objects has been taken
in an early stage of development. In comparison to online
and self-calibration routines the achievable accuracy
is higher and more revisable due to the well-known
target objects and their defined positions. Additionally,
a monitoring algorithm supervises the validity of the
sensor calibration during vehicle fleet operation. For intrinsic
camera calibration and extrinsic sensor calibration
(step 1 and 2) the GT system (rooftop box) is mounted
on a turntable and turned through a defined scenery of
target objects (checkerboards).
Intrinsic camera calibration is carried out with respect to the known literature
based on checkerboards with 7 rows and 10 lines. As quality criteria
for the intrinsic calibration routine a reprojection error of < 0.4 pixel at a
target object coverage rate between 70 % – 80 % is defined.
The “indirect” extrinsic calibration of the sensors using target objects is
necessary, as sensor production tolerances have to be considered. Thus a
“direct” measurement of the sensor position and orientation using a coordinate
measuring machine (CMM) is not feasible. For a pairwise matching
of the sensor’s coordinate systems (= extrinsic calibration) to the central
LiDAR (= reference coordinate system) the normal vectors for each detected
checkerboard are being calculated. A numerical optimization algorithm
aligns these normal vectors for each sensor pair and computes rotation
and translation matrix accordingly. In this way the extrinsic sensor
calibration of the four cameras as well as the two side LiDAR to the central
lidar are carried out.
GT SYSTEM PLUS ACCURATE CALIBRATION ENABLES PLUGAND
PLAY ADAS/AD VALIDATION AND HOMOLOGATION
AVL’s Ground Truth reference system provides a highly precise 360° view
of the environment around the vehicle. The sensor system comes with
accurate
sensor calibration. This offers a great advantage compared to
chassis-mounted
reference sensors and also provides plug-and-play functionality
to our customers. Together with AVL’s worldwide on-site presence
and network of experts our customers receive the best support in their
global data recording and sensor validation campaigns.