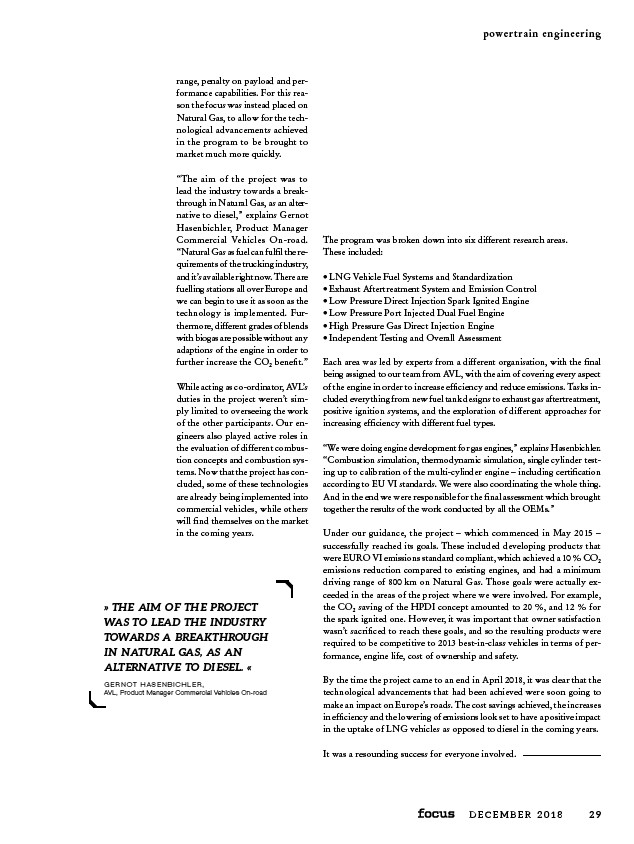
powertrain engineering
D E C EMB E R 2 0 1 8 2 9
range, penalty on payload and performance
capabilities. For this reason
the focus was instead placed on
Natural Gas, to allow for the technological
advancements achieved
in the program to be brought to
market much more quickly.
“The aim of the project was to
lead the industry towards a breakthrough
in Natural Gas, as an alternative
to diesel,” explains Gernot
Hasenbichler, Product Manager
Commercial Vehicles On-road.
“Natural Gas as fuel can fulfil the requirements
of the trucking industry,
and it’s available right now. There are
fuelling stations all over Europe and
we can begin to use it as soon as the
technology is implemented. Furthermore,
different grades of blends
with biogas are possible without any
adaptions of the engine in order to
further increase the CO2 benefit.”
While acting as co-ordinator, AVL’s
duties in the project weren’t simply
limited to overseeing the work
of the other participants. Our engineers
also played active roles in
the evaluation of different combustion
concepts and combustion systems.
Now that the project has concluded,
some of these technologies
are already being implemented into
commercial vehicles, while others
will find themselves on the market
in the coming years.
» THE AIM OF THE PROJECT
WAS TO LEAD THE INDUSTRY
TOWARDS A BREAKTHROUGH
IN NATURAL GAS, AS AN
ALTERNATIVE TO DIESEL. «
GERNOT HASENBICHLER,
AVL, Product Manager Commercial Vehicles On-road
The program was broken down into six different research areas.
These included:
• LNG Vehicle Fuel Systems and Standardization
• Exhaust Aftertreatment System and Emission Control
• Low Pressure Direct Injection Spark Ignited Engine
• Low Pressure Port Injected Dual Fuel Engine
• High Pressure Gas Direct Injection Engine
• Independent Testing and Overall Assessment
Each area was led by experts from a different organisation, with the final
being assigned to our team from AVL, with the aim of covering every aspect
of the engine in order to increase efficiency and reduce emissions. Tasks included
everything from new fuel tank designs to exhaust gas aftertreatment,
positive ignition systems, and the exploration of different approaches for
increasing efficiency with different fuel types.
“We were doing engine development for gas engines,” explains Hasenbichler.
“Combustion simulation, thermodynamic simulation, single cylinder testing
up to calibration of the multi-cylinder engine – including certification
according to EU VI standards. We were also coordinating the whole thing.
And in the end we were responsible for the final assessment which brought
together the results of the work conducted by all the OEMs.”
Under our guidance, the project – which commenced in May 2015 –
successfully reached its goals. These included developing products that
were EURO VI emissions standard compliant, which achieved a 10 % CO2
emissions reduction compared to existing engines, and had a minimum
driving range of 800 km on Natural Gas. Those goals were actually exceeded
in the areas of the project where we were involved. For example,
the CO2 saving of the HPDI concept amounted to 20 %, and 12 % for
the spark ignited one. However, it was important that owner satisfaction
wasn’t sacrificed to reach these goals, and so the resulting products were
required to be competitive to 2013 best-in-class vehicles in terms of performance,
engine life, cost of ownership and safety.
By the time the project came to an end in April 2018, it was clear that the
technological advancements that had been achieved were soon going to
make an impact on Europe’s roads. The cost savings achieved, the increases
in efficiency and the lowering of emissions look set to have a positive impact
in the uptake of LNG vehicles as opposed to diesel in the coming years.
It was a resounding success for everyone involved.