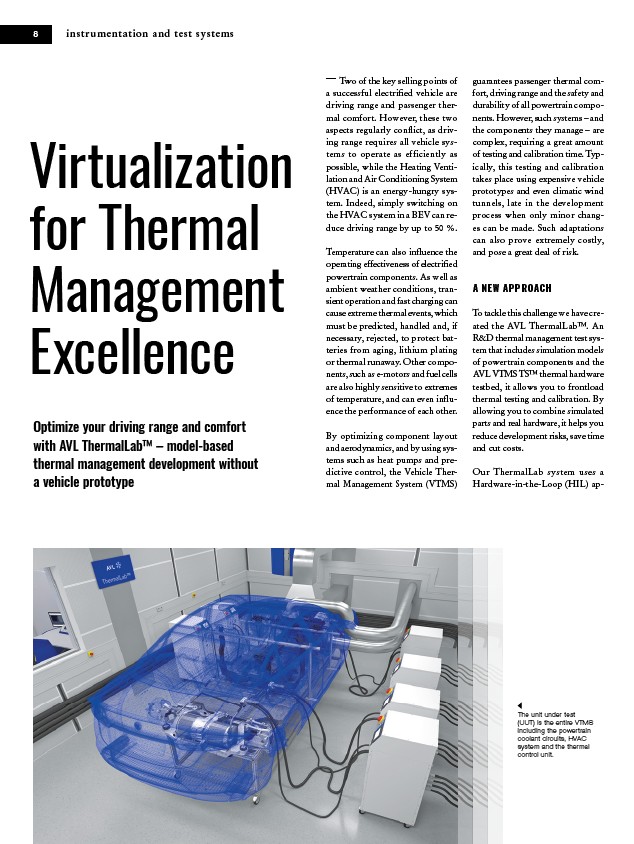
Two of the key selling points of
a successful electrified vehicle are
driving range and passenger thermal
comfort. However, these two
aspects regularly conflict, as driving
range requires all vehicle systems
to operate as efficiently as
possible, while the Heating Ventilation
and Air Conditioning System
(HVAC) is an energy-hungry
system.
Indeed, simply switching on
the HVAC system in a BEV can reduce
driving range by up to 50 %.
Temperature can also influence the
operating effectiveness of electrified
powertrain components. As well as
ambient weather conditions, transient
operation and fast charging can
cause extreme thermal events, which
must be predicted, handled and, if
necessary, rejected, to protect batteries
from aging, lithium plating
or thermal runaway. Other components,
such as e-motors and fuel cells
are also highly sensitive to extremes
of temperature, and can even influence
the performance of each other.
By optimizing component layout
and aerodynamics, and by using systems
such as heat pumps and predictive
control, the Vehicle Thermal
Management System (VTMS)
Virtualization
for Thermal
Management
Excellence
Optimize your driving range and comfort
with AVL ThermalLab™ – model-based
thermal management development without
a vehicle prototype
guarantees passenger thermal comfort,
driving range and the safety and
durability of all powertrain components.
However, such systems – and
the components they manage – are
complex, requiring a great amount
of testing and calibration time. Typically,
this testing and calibration
takes place using expensive vehicle
prototypes and even climatic wind
tunnels, late in the development
process when only minor changes
can be made. Such adaptations
can also prove extremely costly,
and pose a great deal of risk.
A NEW APPROACH
To tackle this challenge we have created
the AVL ThermalLab™. An
R&D thermal management test system
that includes simulation models
of powertrain components and the
AVL VTMS TS™ thermal hardware
testbed, it allows you to frontload
thermal testing and calibration. By
allowing you to combine simulated
parts and real hardware, it helps you
reduce development risks, save time
and cut costs.
Our ThermalLab system uses a
Hardware-in-the-Loop (HIL) ap-
8 instrumentation and test systems
The unit under test
(UUT) is the entire VTMS
including the powertrain
coolant circuits, HVAC
system and the thermal
control unit.