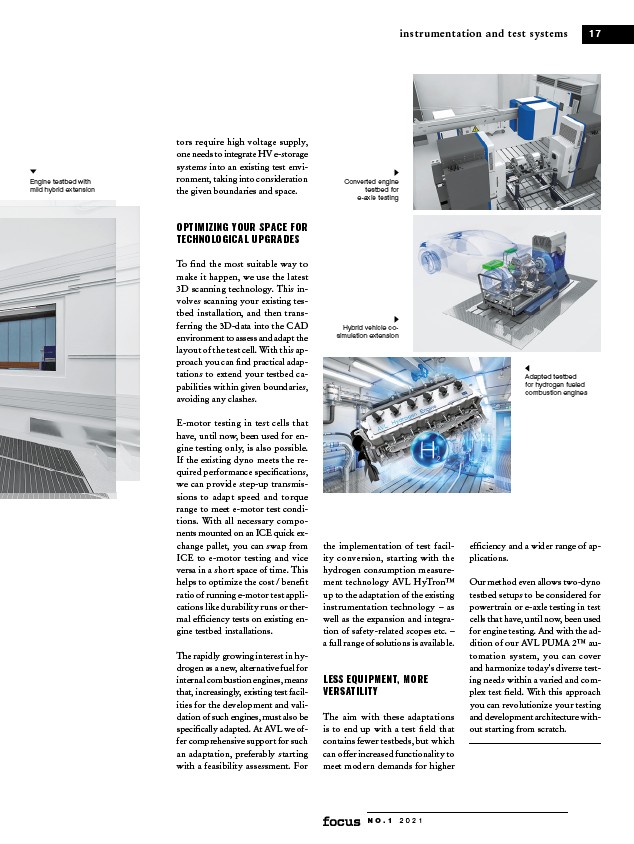
instrumentation and test systems 1 7
N O . 1 2 0 2 1
tors require high voltage supply,
one needs to integrate HV e-storage
systems into an existing test environment,
taking into consideration
the given boundaries and space.
OPTIMIZING YOUR SPACE FOR
TECHNOLOGICAL UPGRADES
To find the most suitable way to
make it happen, we use the latest
3D scanning technology. This involves
scanning your existing testbed
installation, and then transferring
the 3D-data into the CAD
environment to assess and adapt the
layout of the test cell. With this approach
you can find practical adaptations
to extend your testbed capabilities
within given boundaries,
avoiding any clashes.
E-motor testing in test cells that
have, until now, been used for engine
testing only, is also possible.
If the existing dyno meets the required
performance specifications,
we can provide step-up transmissions
to adapt speed and torque
range to meet e-motor test conditions.
With all necessary components
mounted on an ICE quick exchange
pallet, you can swap from
ICE to e-motor testing and vice
versa in a short space of time. This
helps to optimize the cost / benefit
ratio of running e-motor test applications
like durability runs or thermal
efficiency tests on existing engine
testbed installations.
The rapidly growing interest in hydrogen
as a new, alternative fuel for
internal combustion engines, means
that, increasingly, existing test facilities
for the development and validation
of such engines, must also be
specifically adapted. At AVL we offer
comprehensive support for such
an adaptation, preferably starting
with a feasibility assessment. For
the implementation of test facility
conversion, starting with the
hydrogen consumption measurement
technology AVL HyTron™
up to the adaptation of the existing
instrumentation technology – as
well as the expansion and integration
of safety-related scopes etc. –
a full range of solutions is available.
LESS EQUIPMENT, MORE
VERSATILITY
The aim with these adaptations
is to end up with a test field that
contains fewer testbeds, but which
can offer increased functionality to
meet modern demands for higher
efficiency and a wider range of applications.
Our method even allows two-dyno
testbed setups to be considered for
powertrain or e-axle testing in test
cells that have, until now, been used
for engine testing. And with the addition
of our AVL PUMA 2™ automation
system, you can cover
and harmonize today's diverse testing
needs within a varied and complex
test field. With this approach
you can revolutionize your testing
and development architecture without
starting from scratch.
Converted engine
testbed for
e-axle testing
Hybrid vehicle co-
simulation extension
Adapted testbed
for hydrogen fueled
combustion engines
Engine testbed with
mild hybrid extension