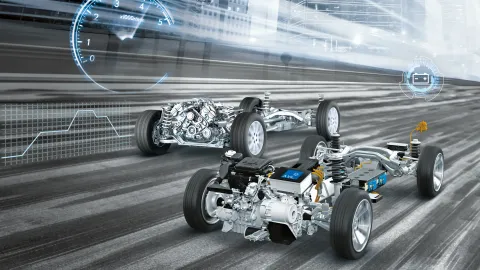
Our control and monitoring system for different testbed applications, enable customers to easily control and monitor a variety of propulsion systems on engine, e-motor, fuel cell, powertrain and vehicle testbeds.
Exact and precise control results in high repeatability of the tests, thereby supporting the efficient integration and calibration of vehicle components.
EMCON 6 is completely integrated into the AVL PUMA 2™ automation system, but it’s also available as an independent system prepared for automatic remote operation.
The automotive industry is facing a number of challenges from increasingly strict global CO2 restrictions, increasing complexity due to new, emerging technologies and the large variety of propulsion systems. Thus, testing on a testbed has become a necessity, not just an option. A state-of-the-art test environment must not only be able to handle this complexity but also enable virtual development for real-world driving conditions along with durability and misuse test capability.
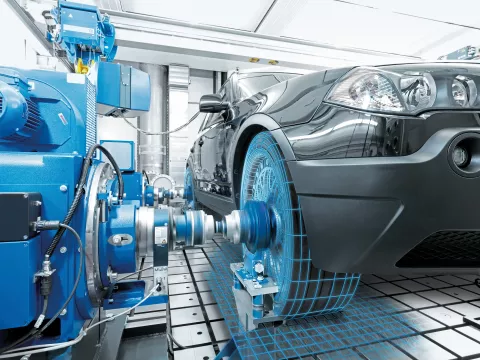
Tried and tested control algorithms enable the exact loading of the propulsion system according to the test requirements. Moreover, EMCON 6 allows you to perform durability tests under real-world driving conditions.
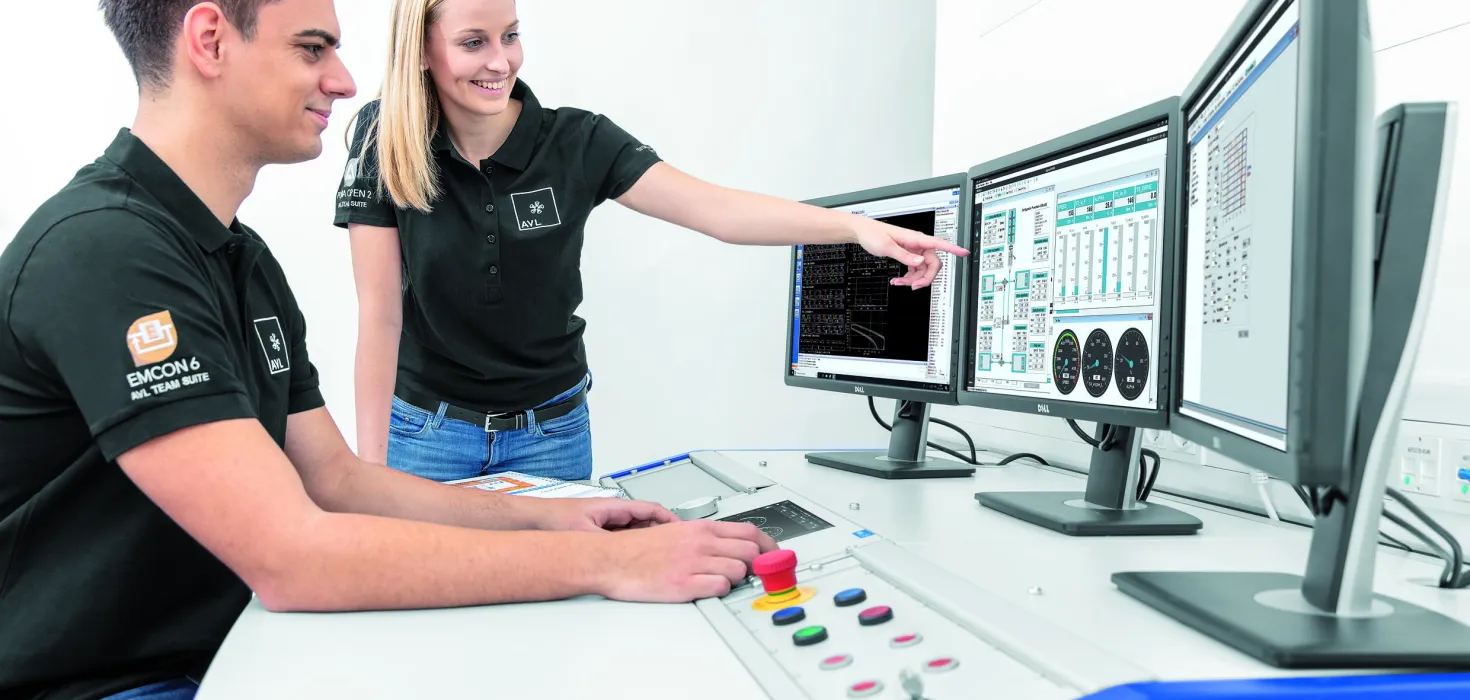
EMCON 6 follows a consistent operation philosophy for fuel cell, e-motor, engine, transmission, powertrain and vehicle testbeds.
Maximum Accuracy
Highly accurate simulated vehicle operation due to easy integration of ISAC 6™ and Testbed.CONNECT models
Top Performance
Reliable, high performance controller with EtherCAT® interface to AVL Dynos at up to 10 kHz
Easy Operation
Easy parameterization with PUMA 2 and test field server AVL PUMA 2™ Share
EMCON 6 is completely integrated into the AVL PUMA 2™ automation system, but it’s also available as an independent system prepared for automatic remote operation.
EMCON 6 Testbed Controller
The EMCON 6 Testbed Controller is a standalone operating, control, and monitoring system for various testbed applications, including combustion engine, electric motor, and e-axle tests. It manages the essential load conditions between the load system (dyno) and the unit under test, and seamlessly integrates into existing environments. Additionally, it supports AVL ISAC™ simulations for e-axle tests and allows integration of custom simulation models via Testbed.CONNECT™ Embedded.
EMCON 6 Dyno Controller
The EMCON 6 Dyno Controller is a standalone control system for individual dynos. It simplifies the operation and control of the load system. With proven control algorithms and high-performance real-time control, this controller is ideal for dynamically managing modern load systems. It serves as an excellent interface for integrating new load systems into existing environments.
Operating Panel TP400
The high-quality 10.1-inch touch display responds to touch gestures and confirms the operator’s selection through haptic feedback. In combination with the two rotary encoders for setpoint adjustment, manual operation of the testbed becomes very secure and extremely intuitive.
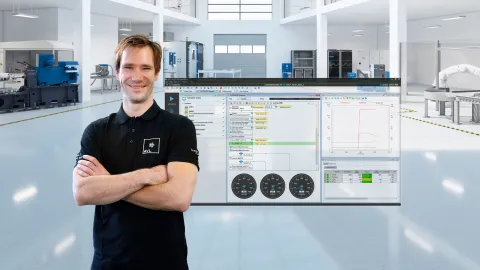
AVL PUMA 2™ is the global industry standard for testbed automation. It is suitable for electrified testbed types as well as for conventional test environments.
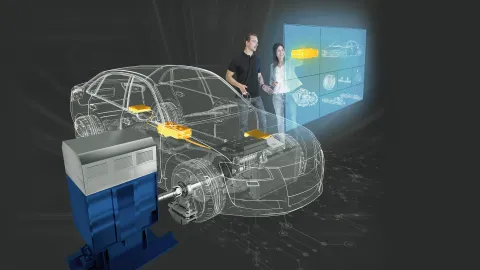
A powerful open execution platform that connects simulation models to the testbed.
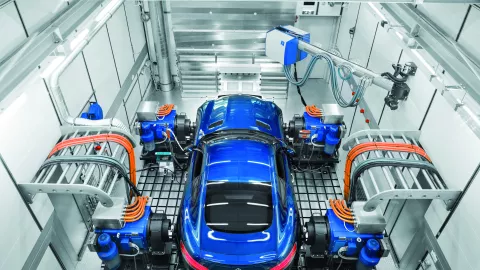
AVL Powertrain TS™ is designed to help you manage the complex validation of ICE-driven vehicles and electric vehicles (EVs) – hybrid EVs, plug-in hybrid EVs, battery EVs, and fuel cell EVs – throughout the development process.
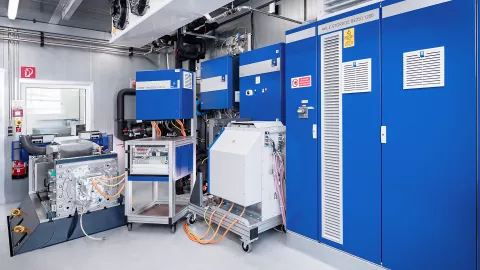
AVL has a wide portfolio consisting of dedicated e-motor test systems, software, tools, and processes to test and validate these modern e-drive systems in shortest time and with highest quality standards.
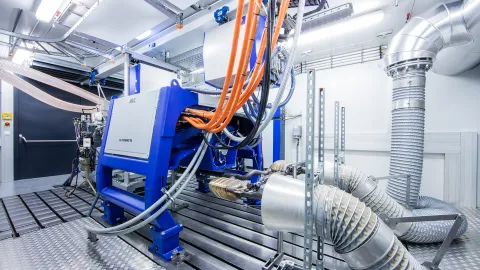
AVL’s hybrid and engine test systems are highly flexible development environments for testing internal combustion engines and their hybrid components.
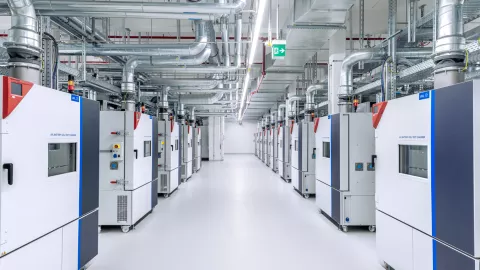
For battery cell testing, we offer complete test systems, stand-alone equipment, or even entire turnkey test labs.