The need to reimagin.
Growing environmental awareness, the need to conserve resources, and great competitive pressure are leading to acceleration.
This acceleration is not only reflected in shorter time-to-market. Rather, it can be felt right down to the first steps of vehicle and component development. New vehicle concepts are becoming increasingly complex as the number of components and their interdependencies grow.

At the same time, the ever-increasing proportion of software in the vehicle cannot be ignored.
It is therefore only logical that this pace cannot be achieved with a purely hardware-driven development. Virtual Twins are one solution. As exact images of individual components, entire systems or even vehicles, they can be used throughout the entire development. Especially since their special feature is the ability to interact with any object inside and outside the system.
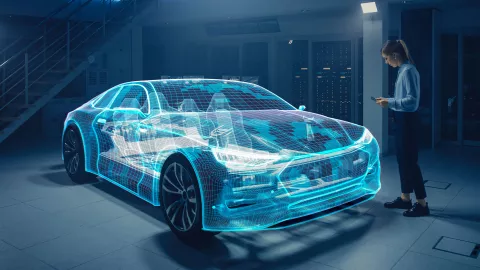

The rapid development of electrification is a challenge for the entire automotive industry. To keep pace here, new paths must be taken. The Virtual Twin is ours. Through simulation development and optimization tasks can be realized in significantly less time.
- Oliver Knaus, Skill Team Leader Solution Management, AVL List GmbH