
The development of vehicle properties such as performance, efficiency, drivability and comfort is becoming increasingly complex due to the wide range of concepts. The individual functions are no longer defined by just one vehicle component. Rather, they are an interaction of several components in a system and associated control software. To ensure the greatest possible development efficiency and quality from the initial idea through design to validation and calibration, engineers need solutions that allow these interactions to be considered together.
Traditionally, vehicle development was strictly divided into disciplines and assemblies. Current trends such as electrification, digitalization, connectivity and driver assistance mean that new approaches have become necessary. Today, the focus is on vehicle attributes and vehicle functions. This requires a holistic, multiphysical approach. Such an approach can only be achieved through virtual analysis, optimization, and validation. Thereby, not only the types of traditional computer-aided engineering (CAE) methods that have expanded (e.g., rainwater separation or sensor contamination), but also the application areas of system simulation.
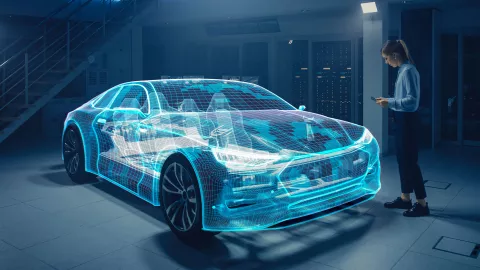
Vehicle attributes include driving and steering behavior, acceleration times, but also air conditioning and range. The latter is particularly crucial for the acceptance of e-mobility.
The range is influenced by a wide variety of factors. In addition to the size of the battery, the efficient use of energy, one's own driving behavior, etc., aerodynamic drag also has a significant influence.
Through recuperation, braking energy can be converted back into electrical energy. If the drag coefficient (cw value) is now reduced by 10%, this can lead to an increase in range of up to 8%.
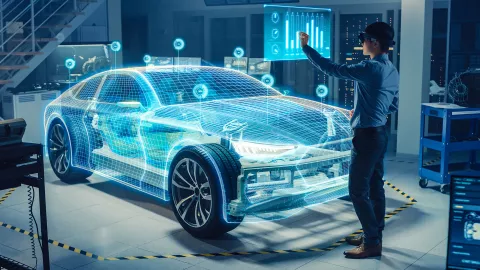
Large battery packs are installed in battery electric vehicles. The weight and its distribution influence the driving and steering behavior.
The various climatic influences must be taken into account when tuning the cabin air conditioning. The challenge here is that passenger comfort and the energy required for it are offset by the loss of range.
Virtual Twins enable you to capture all these interrelationships and analyze them together. As a virtual image of individual components and systems or even entire vehicles and with the inclusion of their environment, they are an efficient tool for driving development forward.
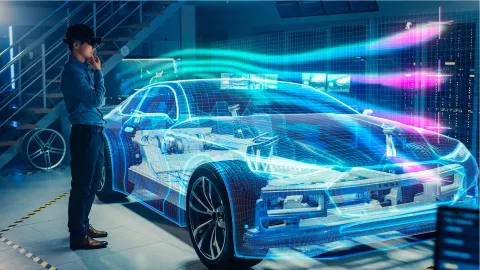
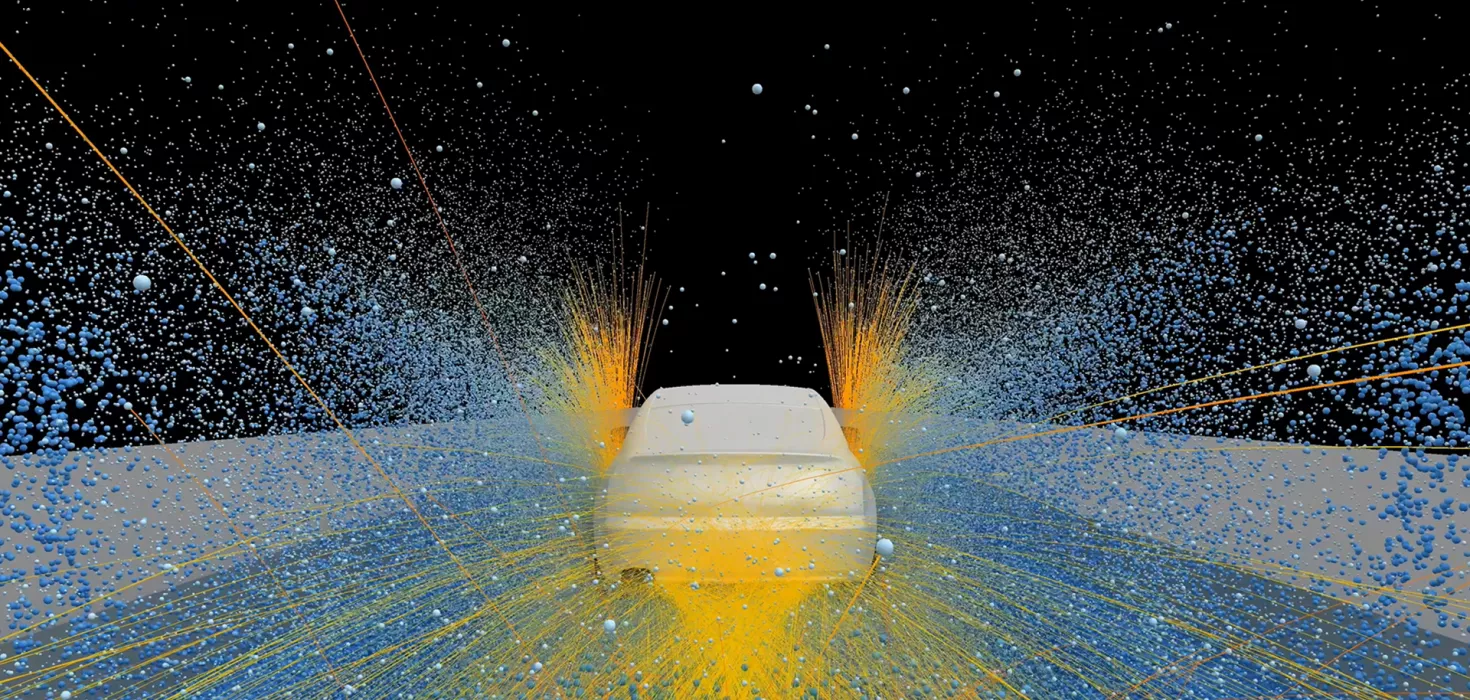
Drivers are relying more and more on the latest technologies in ADAS and AD systems. In the process, the number of sensors and cameras required for this continues to increase.
In order to provide maximum safety, the sensors and cameras must function reliably. Using our simulation solution, you can combine turbulent aerodynamics with particle-based simulation to predict contamination on the vehicle surface. Virtual testing allows you to optimize the design of the vehicle and the positioning of the sensors as early as the concept phase.
Numerical simulations with complete vehicle models enable you to significantly reduce experimental effort. Virtual Twins that exist before a physical model allow you to make predictions very early on in the V-development process. This increases your development quality and shortens the development time.
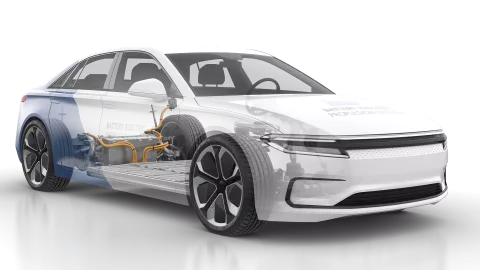
Achieve the Balance Between Energy Efficiency and Driving Experience
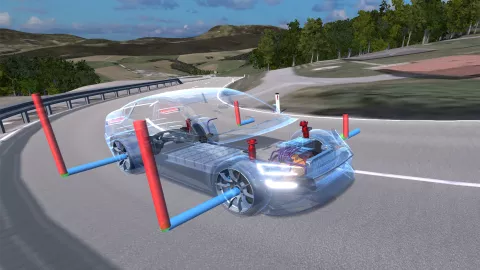
In order to combine outstanding driving characteristics such as performance, ride, handling and ride comfort with the goals defined in the concept phase, like energy efficiency and consumption, the overall system must be considered.
Optimization of the Overall Vehicle System
By integrating simulation into the development process it is possible to study the interaction of the individual components in the overall system. This gives you the opportunity to analyze and ideally balance vehicle attributes in the event of conflicting goals.
Simulation supports you with:
- Vehicle conception
- Assessment of vehicle dynamics
- Development of vehicle functions
- Energy management at overall vehicle level
- Optimization of lap times in racing
Unify HVAC, Thermal, Mechanical, and Electrical Systems With Simulation
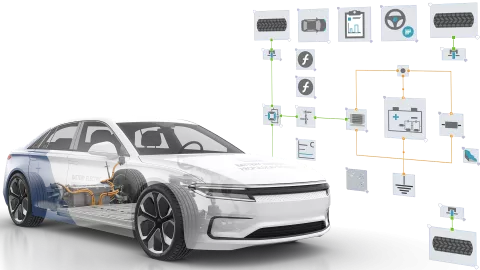
Engineers are facing completely new challenges in terms of thermal management when developing electric vehicles. Whereas the waste heat from the internal combustion engine was previously used for air conditioning in the passenger compartment, the battery must be used for this in electrified vehicles. This in turn is detrimental to the range.
Optimize Thermal and Electrical Energy Management
Energy management has increased in complexity with electrification. The rapidly growing market is shortening the development time. Considering the system at overall vehicle level is becoming more and more important here.
- Compartment comfort systems: heating, ventilation, and air conditioning
- Thermal management systems for components
- Alignment of electrics and electronics
(H4) Lorem Ipsum
Lorem ipsum dolor sit amet, consetetur sadipscing elitr, sed diam nonumy eirmod tempor invidunt ut labore et dolore magna aliquyam erat, sed diam voluptua. At vero eos et accusam et justo duo dolores et ea rebum. Stet clita kasd gubergren, no sea takimata sanctus est Lorem ipsum dolor sit amet. Lorem ipsum dolor sit amet, consetetur sadipscing elitr, sed diam nonumy eirmod tempor
(H4) Lorem Ipsum
Lorem ipsum dolor sit amet, consetetur sadipscing elitr, sed diam nonumy eirmod tempor invidunt ut labore et dolore magna aliquyam erat, sed diam voluptua. At vero eos et accusam et justo duo dolores et ea rebum. Stet clita kasd gubergren, no sea takimata sanctus est Lorem ipsum dolor sit amet. Lorem ipsum dolor sit amet, consetetur sadipscing elitr, sed diam nonumy eirmod tempor
Optimization of the Vehicle Body Through Simulation
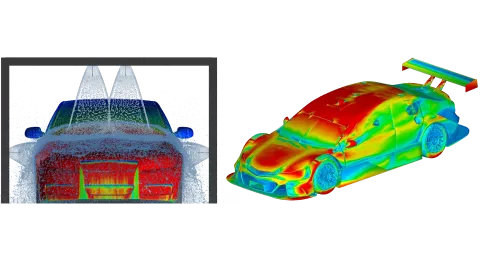
The body of a vehicle fulfills a wide variety of tasks. Responsible for the external appearance, it also influences the acoustic behavior of the vehicle to the outside (radiation) and to the inside (interior noise). However, its most important task is to protect passengers and cargo from all external influences.
Virtually Study Sensors and Camera Soiling
Apply computational fluid dynamics (CFD) and particle-based simulation solutions (SPH) to calculate and visualize flow patterns around your vehicle.
- Simulation of water – this includes wading and rainwater
- Simulation of accumulation of snow on the vehicle
- Simulation of soiling of windshields, mirrors, and sensors
(H4) Lorem Ipsum
Lorem ipsum dolor sit amet, consetetur sadipscing elitr, sed diam nonumy eirmod tempor invidunt ut labore et dolore magna aliquyam erat, sed diam voluptua. At vero eos et accusam et justo duo dolores et ea rebum. Stet clita kasd gubergren, no sea takimata sanctus est Lorem ipsum dolor sit amet. Lorem ipsum dolor sit amet, consetetur sadipscing elitr, sed diam nonumy eirmod tempor
(H4) Lorem Ipsum
Lorem ipsum dolor sit amet, consetetur sadipscing elitr, sed diam nonumy eirmod tempor invidunt ut labore et dolore magna aliquyam erat, sed diam voluptua. At vero eos et accusam et justo duo dolores et ea rebum. Stet clita kasd gubergren, no sea takimata sanctus est Lorem ipsum dolor sit amet. Lorem ipsum dolor sit amet, consetetur sadipscing elitr, sed diam nonumy eirmod tempor
The mobility revolution is in full swing. This is not just about developing new, more sustainable propulsion systems. Rather, the entire development process is in upheaval - with simulation taking the lead.
Right now, it's important to understand the challenge that each of us - OEMs and suppliers alike - face when it comes to pushing the boundaries of both our design process and our engineers. As the number of different systems grows, departments and team structures are changing. We understand that. At AVL, we go through these processes as well, because we are not just software developers. We are also engineers and therefore users. We implement our knowledge in intuitive workflows, generators, wizards, and evaluations in our software and projects.
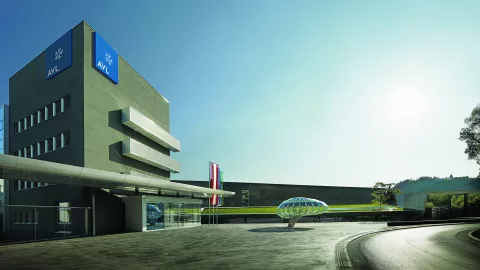
We are your global partner in realizing the mobility of the future. A mobility characterized by its minimal impact on the environment. We offer you simulation solutions ranging from component to system analysis. As we are deeply integrated in the development process, our software solutions - tools and projects - enable you to master the challenges of virtualization.
75+
years of experience
in 26
countries worldwide
12,200
employees worldwide
68%
engineers and scientist