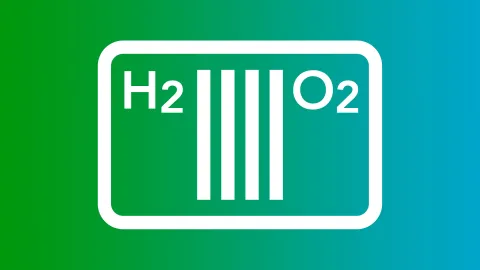
Neuerungen im Bereich der Simulation von Brennstoffzellen und Elektrolyseuren
Die Erstellung von Simulationsmodellen für PEM-Brennstoffzellensysteme kann anspruchsvoll sein. Sie erfordert grundlegende Kenntnisse über die Systemanordnung, die verwendeten Komponenten und deren Dimensionierung, damit die Modelle den tatsächlichen Anwendungsfall und Leistungsbereich des Stacks bzw. des Systems zuverlässig abbilden. Darüber hinaus sind mehrere grundlegende Regelungsfunktionen erforderlich, um das Gesamtsystem unter transienten Lastbedingungen zu betreiben. AVL CRUISE™ M bietet Ihnen mit dem PEMFC System Generator eine komfortable Möglichkeit, den Modellaufbau und die Parametrisierung zu beschleunigen. Der Ausgangspunkt für den kompletten Modellaufbau ist die Eingabe von lediglich zwei Parametern: die aktive Zellfläche und die Anzahl der Zellen im Stack. Damit sind Sie startklar und können das Modell erstellen. Falls gewünscht, gibt es eine Reihe von weiteren Eingabeoptionen, um die Modellerstellung nach Ihren Bedürfnissen zu gestalten. Sobald das Modell erstellt ist, haben Sie für weitere Anpassungen vollen Zugriff auf alle Komponenten. Dazu gehört auch der Zugriff auf den Code, der für die Steuerung der Anlage zuständig ist, und die Möglichkeit, flexibel jedes instationäre Lastprofil zu definieren
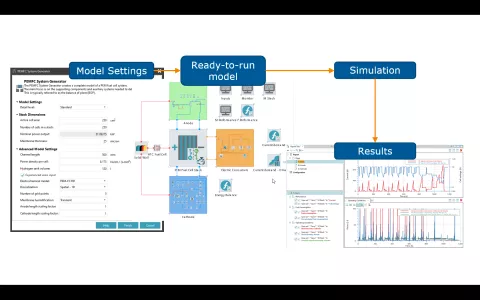
Eine Möglichkeit zur Verringerung der Masse und der thermischen Trägheit von Brennstoffzellenstacks besteht darin, von maschinell bearbeiteten Bipolarplatten auf gestanzte Blechplatten umzusteigen. Letztere weisen dünnere Wände und gleichzeitig ein größeres Verhältnis von aktivem Kanalquerschnitt und Kühlquerschnitt auf.
In der aktuellen Version von CRUISE M können Sie diese Art von Bipolarplattengeometrien flexibel simulieren. Sie müssen lediglich die Kanalbreite, die Plattenhöhe und die Blechdicke auf der Anoden- und Kathodenseite angeben und schon können Sie loslegen. KPIs für Stapel- und Bipolarplatten-, Kanal- und Kühlvolumen geben Ihnen sofortiges Feedback über die Konsistenz Ihrer Eingaben. Der Unterschied zwischen bearbeiteten Bipolar- und Blechplatten wird in einem speziellen Installationsbeispiel erläutert, das die 3D-Temperaturverteilungseffekte im Stack vollständig berücksichtigt. Dieses Beispiel ist sofort einsatzbereit und dient als Ausgangspunkt für Ihre kundenspezifischen Simulationen, z. B. für die Analyse der Auswirkungen unterschiedlicher Betriebstemperaturen auf die Effizienz der Wasserstoffumwandlung im Stack.
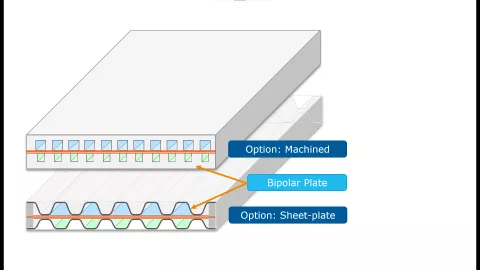
Brennstoffzellenstacks sind eine Anordnung einzelner Zellen, die jeweils aus Bipolarplatten, Gasdiffusionsschichten und der Membran bestehen. Jede Schicht ist von Natur aus wärmeleitend. Selbst wenn das thermische Verhalten des Stapels pauschal modelliert wird, ist es wichtig, die anisotrope Wärmeleitung sowohl in der Ebene als auch in der dazu senkrechten Richtung zu berücksichtigen.
Wenn Sie ein 3D-Stackmodell in CRUISE M ausführen, können Sie zwischen isotroper und anisotroper Wärmeleitung wählen. Außerdem haben Sie die Möglichkeit, die berechnete Wärmeleitung, die aus den echten Materialdaten abgeleitet wurde, zu skalieren. Die Skalierungswerte können auch mit dem CRUISE M Datenbusnetzwerk verbunden werden. Dies gibt Ihnen volle Flexibilität bei der Identifizierung von Modellparametern sogar während einer laufenden Simulation. Zur Veranschaulichung der Wärmeleitungsfunktionalitäten steht ein spezielles Installationsbeispiel zur Verfügung, einschließlich eines Vergleichs der räumlichen Temperaturverteilung während der Abkühlphase für einen Stack mit isotroper und anisotroper Wärmeleitung.
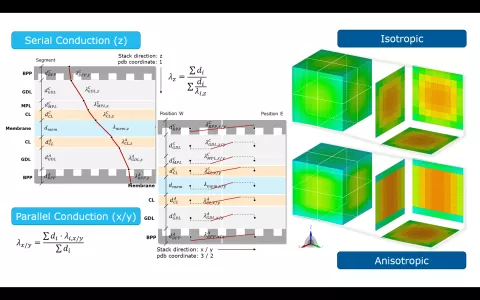
Die Simulation von Festoxid-Brennstoffzellen- und Elektrolyseursystemen erfordert nicht nur die Berücksichtigung des Transports gasförmiger Spezies, sondern auch von Spezies in der flüssigen Phase, da Elektrolyseurkomponenten typischerweise mit flüssigem Wasser gespeist werden, während teilweise oder vollständig gasförmige Spezies diese Komponenten verlassen.
Diese Version von CRUISE M ermöglicht es, die Verfügbarkeit von flüssigen Spezies im thermodynamischen Gasnetz zu berücksichtigen. Gasförmige und flüssige Fluidkomponenten werden durch das gesamte Netzwerk transportiert, wobei Phasenübergangsprozesse in den Zustandskomponenten, wie Plenum und quasidimensionales Rohr (QDP), modelliert werden. In der aktuellen Version von CRUISE M wird das Flüssigkeitstransportmodell mit einem eigenen VLE (Vapor-Liquid Equilibrium) Strömungsnetzwerk für Temperaturbereiche validiert, in denen die spezifischen Enthalpien linear über die Temperatur verlaufen, d.h. für Betriebspunkte deutlich unterhalb des kritischen Punktes.
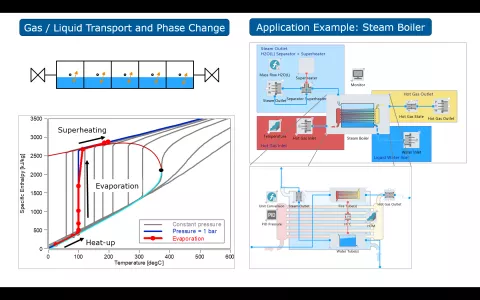
Das PEM-Brennstoffzellenmodul von AVL FIRE™ M wurde erweitert, um auch die Simulation von Anion Exchange Membrane (AEM) Elektrolyseurzellen abzudecken. AEM-Elektrolyseure sind alkalische Elektrolyseure, bei denen das zwischen den Elektroden befindliche Diaphragma durch eine Ionenaustauschmembran ersetzt ist. Obwohl AEM-Elektrolyseure mit reinem Wasser betrieben werden können, werden die Zellen normalerweise mit einer schwachen wässrigen Elektrolytlösung gespeist, um die Leistung zu erhöhen. Häufig werden KOH (Kaliumhydroxid) oder NaOH (Natriumhydroxid) als Elektrolyte verwendet. Der Ladungstransport durch die Membran erfolgt durch den Transport von Anionen (OH-) und nicht von Kationen (oder Protonen). Ein häufig verwendetes Material für die Anionenaustauschmembranen ist Hexamethyltrimethylammonium-funktionalisiertes Diels-Alder-Polyphenylen (HTMA-DAPP).
Die größten Unterschiede bei der Modellierung von AEM- und PEM-Elektrolyseuren ergeben sich aus der Existenz des flüssigen Elektrolyten. Daher löst FIRE M zusätzliche Transportgleichungen für die Massenbilanz der flüssigen Ionen und die Gleichung zur Erhaltung der flüssigen Ladung im flüssigen Elektrolyten. An der Grenzfläche zwischen dem flüssigen Elektrolyten und dem Ionomer wird ein Stofftransportansatz verfolgt, der den Ein- und Austritt von Anionen in die Membran ermöglicht. Um die Verteilung der Ionenkonzentration genauer zu berechnen, wird eine zusätzliche Ionentransportgleichung in der Ionomerphase der Membran gelöst. Die Ionenkonzentration wird auch in die Butler-Volmer-Gleichung aufgenommen, um eine schnellere Sauerstoffentwicklungsreaktion bei höheren Anionenkonzentrationen zu berücksichtigen.

In der aktuellen Version wurde das Brennstoffzellenmodul von FIRE M um die Simulation von Hochtemperatur-PEM-Brennstoffzellen erweitert. Der Hauptunterschied zur Niedertemperatur-PEM-Brennstoffzelle ist die Betriebstemperatur, die typischerweise im Bereich von 130-180°C liegt, und damit das Fehlen von flüssigem Wasser. Aufgrund der hohen Betriebstemperatur kommt ein anderes Membranmaterial zur Anwendung. Die gebräuchlichsten Materialien sind poröse Membranen auf Polybenzimidazolbasis (PBI), die mit Phosphorsäure dotiert sind. Die Ionenleitfähigkeit wird von der Phosphorsäure bereitgestellt und ist normalerweise nur von der Temperatur abhängig. In der Phosphorsäure können die verschiedenen Spezies die Membran durchqueren und im Falle von O2 und H2 zu parasitären Reaktionen auf der gegenüberliegenden Seite führen, welche in dem vorliegenden Modell berücksichtigt werden. Alle Degradationsmechanismen in der Katalysatorschicht werden in der gleichen Weise modelliert wie bei der Niedertemperatur-PEM-Brennstoffzelle.
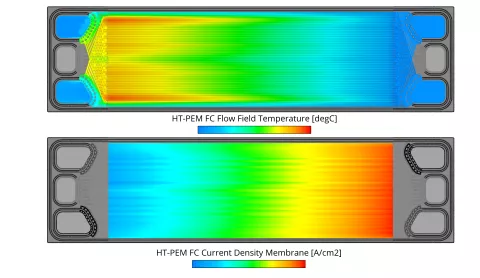