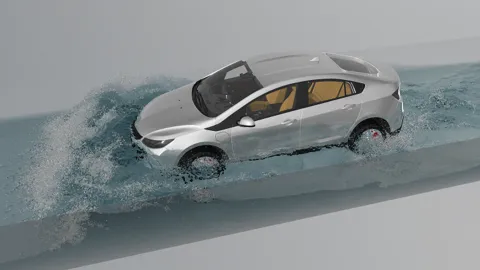
Design for vehicle water management is an important part of the vehicle development process that still heavily relies on physical testing. Traditional CFD methods cannot handle full-scale water management applications and deliver reliable results within reasonable time frames.
The meshless SPH method with high-performance implementation, on the other hand, makes a perfect fit for large-scale and highly dynamic cases, typically encountered in vehicle water management.
Vehicle design for water management still relies on complex physical testing for use cases like wading. Such climatic wind tunnel experiments are not only expensive, it is also hard to reproduce real-world conditions like heavy rain or snow. In Addition, it can be difficult to observe and measure the critical phenomena. For these reasons, relying solely on testing can lead to costly late-stage rectifications.
While model preparation can be time consuming in conventional CFD software, a particle-based solution allows for simple meshless modelling. SPH is the leading solution for configurations that feature large domains, physical times, fee-surface and highly dynamic liquid dominated flows. This complexity level is typical for water management applications where mesh-based methods are difficult to apply or very expensive.
Meshless virtualization allows for frontloading by gaining actionable insights that impact vehicle water management early in the development process.
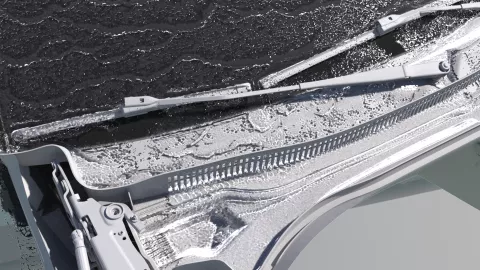
Avoid Late Design Changes
Reveal potential risks early on. This helps you avoid late detection of failure modes and expensive design changes.
Rely on Photorealistic Visualization
Photorealistic visualization and virtual sensors give you detailed insight into every component of the vehicle.
Make Model Preparation Easy
Particle-based solution implies that there is no need for meshing, simple discretization of complex domains, handling complex boundary evolution as well as modeling complicated physics in a relatively simple manner.
Work with Fast Design Iterations
Gain actionable insights fast, enabling you to impact the design at early development stages, revealing potential risks helps you avoid late detection of failure modes and expensive design changes.
Master Complexity
Take into account the complexity of large domains, physical times, and highly dynamic flows that are hard to apply/inapplicable using traditional CFD.
The geometry is easily imported into the solution via drag and drop, even low-quality CAD data is not an issue, being readily handled by the particle-based approach. There is no need for tedious pre-processing work and meshing.
The intuitive GUI makes the simulation setup streamlined and straightforward, a distinctive unique user experience enabling also non-CFD experts to explore and optimize design for water management.
You can easily use photorealistic visualization and virtual sensors to gain detailed insight into every component of the vehicle. Revealing potential risks helps you avoid late detection of failure modes and expensive design changes.
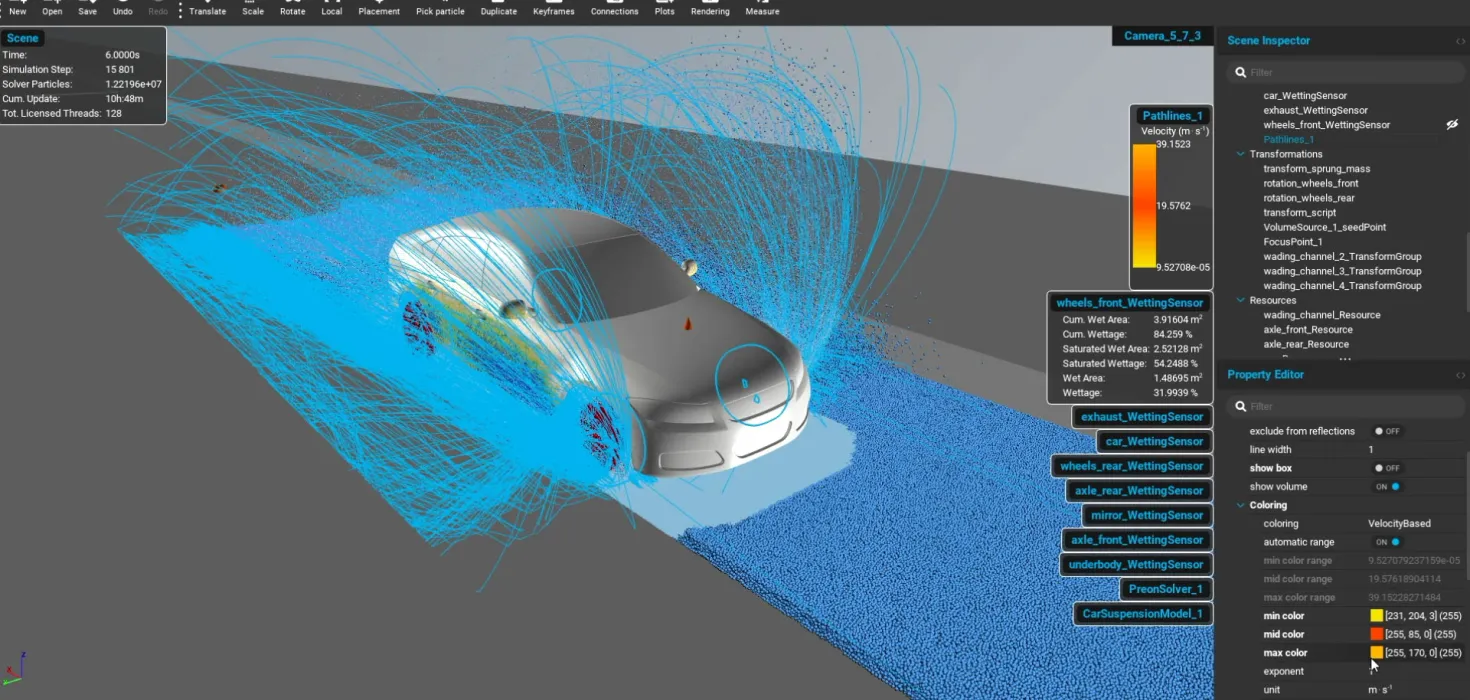
Take advantage of the market leading SPH simulation solution for vehicle water management.
Fastest CAD-to-Results Time
Faster results expedite design iterations and reduce lead time. Take simulation data-driven decisions, influencing design before the first prototype.
Unique UX
Our solution's GUI is so intuitive that engineers with no CFD experience can use it effectively. This helps bridge the gap between analysts and designers.
Photo-realistic Visualization
In-tool rendering, post-processing, and photorealistic visualizations provide clear, actionable engineering insights. This powerful data visualization helps users make timely and informed decisions.
Efficient Handling of Multiscale Phenomena
The proprietary Continuous Particle Size (CPS) approach enables highly adaptive resolution. Increase particle density in regions of interest, and save computational resources elsewhere.
Multi-GPU Capability
The addition of multi-GPU support expands available memory by leveraging multiple GPUs simultaneously. The synergy between memory saving features (CPS, dynamic sampling, adaptive sampling) and the multi-GPU support make it possible to execute simulations not possible before due to memory constraints.
Continuous Particle Size (CPS)
CPS enables the use of a much larger size ratio between the coarsest and finest particle sizes in the simulation, meaning that the number of particles in the simulation can be significantly reduced.
Dynamic and Adaptive Sampling
PreonLab offers the ability to connect tensor fields to solid objects with dynamic sampling enabled. The “Preon Solver” and “Solid Volume Solver” objects offer a continuous particle size option, which includes adaptive sampling, refinement, and coarsening.
Snow Solver
Snow in contrary to fluids has quite a large variety of dynamics. An elasto-plastic model has been proven to be quite powerful to model snow. PreonLab treats snow as a complex material, allowing for accumulation and a wide range of subscales to be realized.
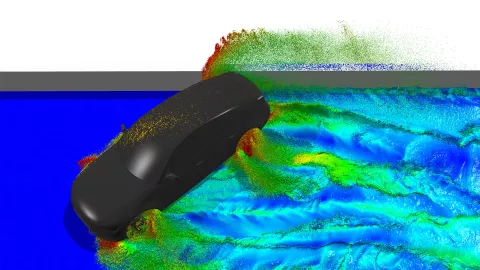
The difference between classic CFD and PreonLab is quickly explained. Classical CFD is based on mesh creation, for PreonLab a different approach was chosen: Smoothed-Paritcle Hydrodynamics (SPH) is the basis of the revolutionary PREON® technology.
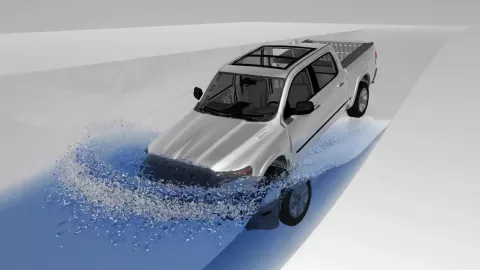
Vehicle water management is a critical component of design, which traditionally has heavily relied on costly physical testing. Whereas conventional CFD is hardly applicable due to underlying modeling complexity and extremely high computational costs, SPH technology has virtually revolutionized water management simulation.
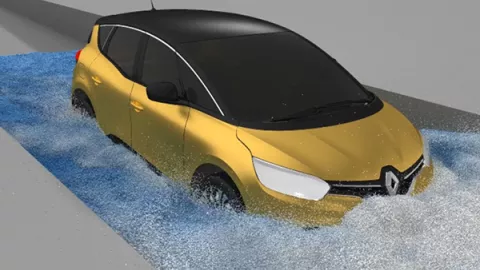
Water management is an important aspect of vehicle design. It includes everything from soiling and wading to splashing and the impact this has on the vehicle's aerodynamics. Even the vehicle's windshield wipers are part of it, as is the investigation

Vehicle water management is a challenging engineering problem to address, but the right development tool can make the process more efficient and enjoyable for the engineer.