In contrast to classical CFD, the simulations in PreonLab are meshless. This not only simplifies model creation. It gives you short and powerful turnaround times when simulating Newtonian and non-Newtonian fluids. Regardless of whether you want trend analysis or precise predictions.
Ease of use was and still is particularly important in the development of the software. Thus, it was designed so that every user can use it intuitively in his daily work with a little training.
The goal has always been: to make development as efficient as possible without compromising on the quality of the results.
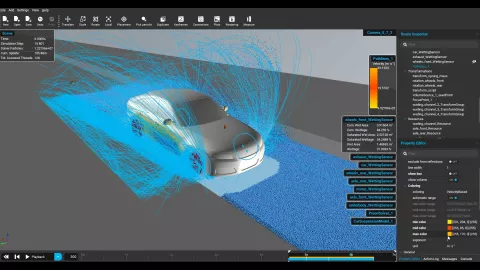
ATZextra – Mesh Free CFD Technology Revolutionizes Water Wading Analysis
Smoothed Particle Hydrodynamics (SPH) simulation is a promising mesh-free CFD technology that has revolutionized water wading analysis in recent years. AVL and Magna present a validation study that demonstrates predictive capability and efficiency of SPH-based virtualization. Leveraging virtual passenger car testing, development time and reliance on physical prototypes can be significantly reduced.
AVL Customer Case Study - Simulation-based Development of Functional Oil Distribution in Electric Axle Systems
Electric axle systems play an important role in vehicle electrification. Due to their compact design, they can be used in all vehicle segments with hybridized or all-electric powertrains.
AVL Customer Case Study - Water Wading Simulation
“Water wading” is a standard test in vehicle development. Water must not enter critical areas endangering e.g., battery packs, electric components or the air intake. Forces caused by the water should not damage the car body or float the vehicle.