Preventing Thermal Runaway: Simulation as a Tool for Improved Battery Cell Safety
- Blog
A dreaded phenomenon in battery development is the thermal runaway of the battery cell. It describes complex electrochemical reactions within a battery cell (as a result of various triggers) that lead to a strong release of heat and the associated increase in temperature, off-gassing of the cell and ejection of hot particles from the cell. At the module or pack level, this heat release can spill over to neighboring cells, creating a dangerous chain reaction – a process known as thermal propagation.
Batteries can be compared to the fuel tank of a vehicle with an internal combustion engine. Compared to these, however, battery packs only store the equivalent of approx. 8 liters of fuel. Due to the efficiency of electric powertrains, this comparatively small amount of energy is enough to drive the vehicle a few hundred kilometers. However, in the event of a malfunction or an accident, this amount of energy is also sufficient to cause a thermal runaway.
Should such a situation occur, it is important to minimize the damage and stop or delay the process in order to ensure the safety of the passengers. For this reason, there are regulations such as GTR20 (Global Technical Regulations (GTRs) | UNECE), which stipulate that in the event of a thermal runaway, a warning light must illuminate in the cockpit of the vehicle and passengers must have at least five minutes to safely exit the vehicle after the warning signal appears.
The development of safety measures is crucial to minimize these risks and ensure the safety and acceptance of electric vehicles.
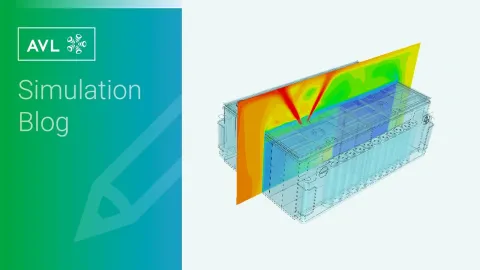
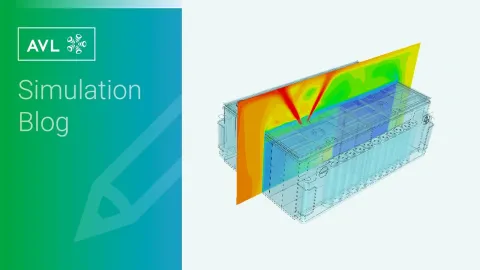
Assuring the safety of batteries is a key aspect in the development of battery packs and electric powertrains. On the one hand, manufacturers must fulfill regulatory requirements and prove that their products pass thermal runaway tests. On the other hand, the occurrence of malfunctions – or in the worst case battery fires – can lead to recalls in the media and a loss of image for car manufacturers or suppliers. Certification tests, similar to crash tests for vehicle safety, are therefore essential. Products that do not pass these tests must not be brought onto the market.
Virtual tests using 1D or 3D simulation software can be helpful in generating reliable information in the early development phases of a new battery design. These enable development engineers to make early statements about the behavior of a design. Due to the detailed temporal and spatial resolution of the calculation results, insights and findings are sometimes possible that cannot be represented in a hardware test. This allows developers to estimate at an early stage whether a design will pass the certification tests.
Countermeasures to Prevent Thermal Propagation or Mitigate Consequences
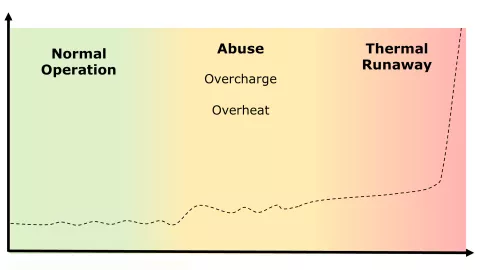
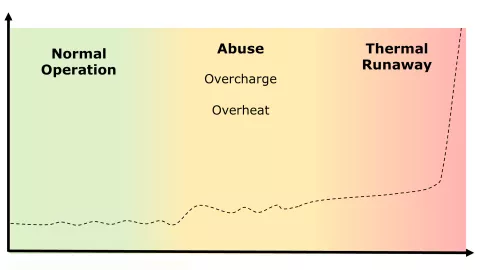
There are three trigger mechanisms that can cause a battery cell to fail:
1. Overheating due to problems with the cooling system or an external heat influence.
2. Overcharging, caused by a malfunction in the battery management system, which leads to an uncontrolled supply of current and chemical side reactions.
3. Mechanical damage, for example due to an accident.
All three mechanisms ultimately lead to damage to the separator, causing an internal short circuit. Suitable countermeasures can prevent the triggers or bring the effects under control. A distinction is made between two types of measures – active safety and passive safety.
Active safety includes measures such as cooling and degradation management, which aim to ensure that the battery is always in a safe operating state.
Passive safety, on the other hand, refers to minimizing the consequences of a thermal runaway once it has already occurred. This involves ensuring the safety of the battery, even if a fault or accident occurs, through appropriate design and strategies.
The use of simulation solutions such as AVL CRUISE™ M and AVL FIRE™ M plays a crucial role in optimizing battery safety. Not only does this allow a potentially dangerous hardware test to be transferred to a safe, virtual environment, it also opens up possibilities and insights that cannot be achieved on the test bench.
The aim is to keep the battery in the “comfort zone” and to optimize the design so that a thermal runaway does not occur in the first place. Potential design problems can be detected and avoided at an early stage.
Optimizing the Battery Design: Mapping Effects and Minimizing Risks
A detailed Virtual Twin allows various scenarios to be run through in the simulation. For example, it is possible to find out whether a design meets the required regulations (e.g. GTR20) or whether additional safety precautions are necessary. Examples here would be the implementation of additional rupture disks to allow the released gas to escape safely.
Thanks to its fast calculation times compared to 3D simulations, CRUISE M is very well suited in early design phases to generate initial assessable results within seconds or minutes – even if no CAD data is available at this stage. Avoiding a thermal runaway starts with the right control strategy and early detection of critical points. CRUISE M can provide valuable insights here thanks to its electrochemical model and enable timely intervention.
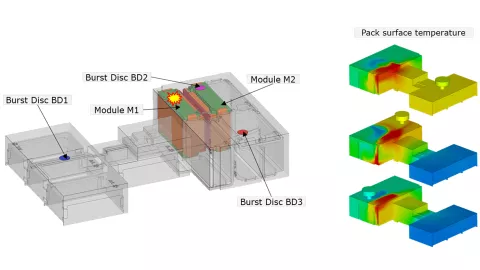
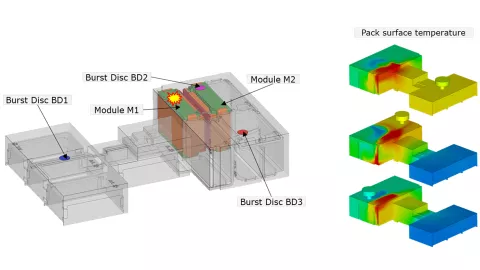
Finally, FIRE M makes it possible to take all relevant physical phenomena into account at component level in the later phases of development. By taking into account phenomena such as the emission of hot gases and particles as well as fusible components such as rupture discs, the safety of the battery can be increased and potential risks minimized. A combined risk assessment helps to identify different hazard factors and understand how they can influence each other to ensure the safety of the battery.
In the world of battery technology, engineers are facing new challenges, but also new opportunities to optimize safety. One emerging trend is the demand from manufacturers for concepts that go beyond the standard 5-minute limit. The aim is to realize so-called “no propagation” concepts, in which no further chain reaction occurs as a result of a thermal runaway in one or more battery cells. This industry requirement reflects the constant desire to raise the safety of batteries to a higher level and to meet the requirements for a reliable and low-risk energy source. By using state-of-the-art simulation technologies such as CRUISE M and FIRE M, we are well on the way to meeting these demands and paving the way for a safer future of electromobility.
Stay tuned
Don't miss the Simulation blog series. Sign up today and stay informed!
Learn More About This Topic
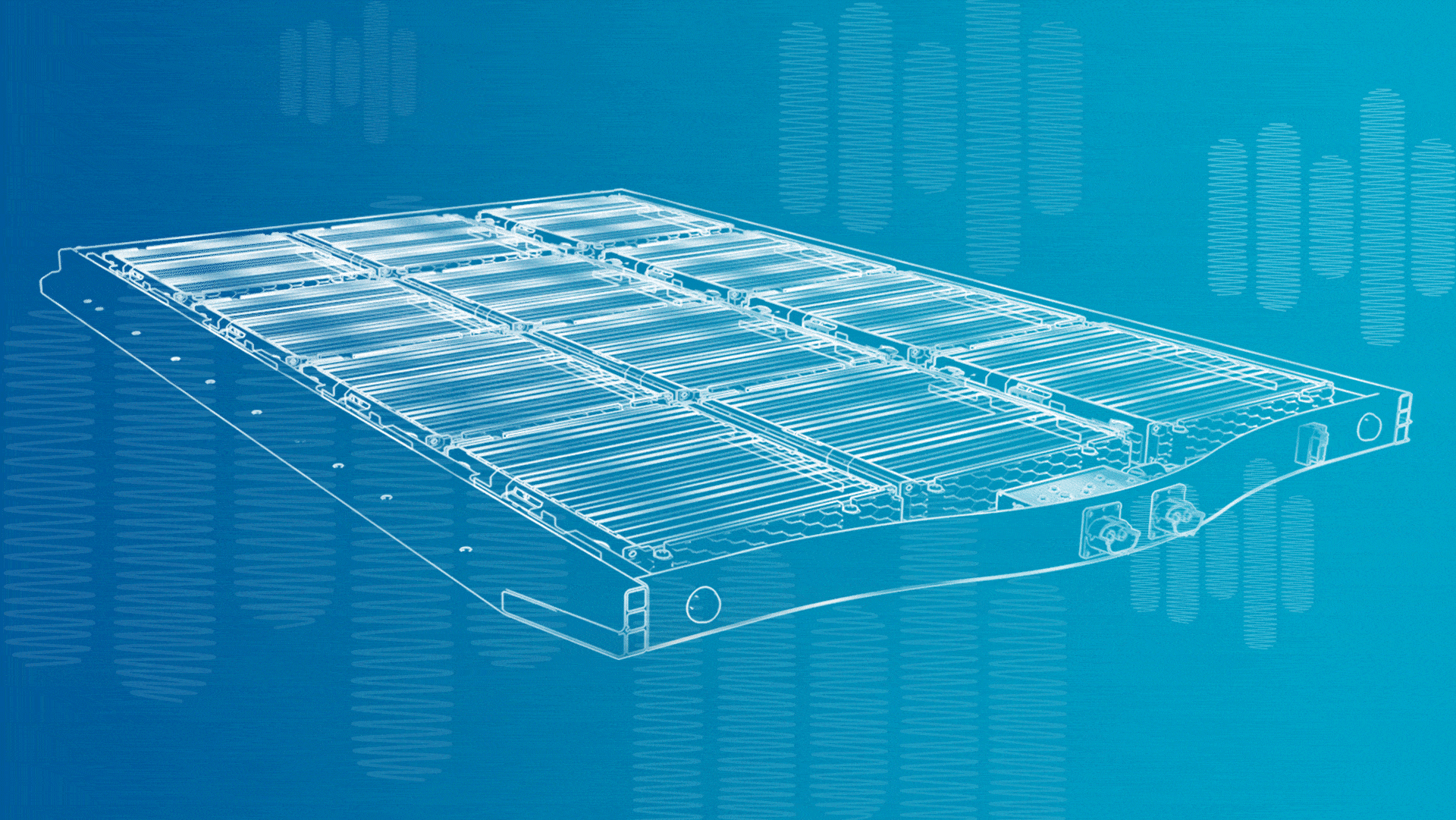
In many markets, battery electric vehicles have yet to achieve the same level of acceptance as combustion engine vehicles. To make them more competitive, it is essential to reduce the cost of EVs and build confidence in their safety.
Stay tuned for the Simulation Blog
Don't miss the Simulation blog series. Sign up today and stay informed!