‘If you don’t actively attack risks, they will actively attack you !’ (Tom Gilb) According to that, we embed our services for equipment into your risk management. The goal is to reduce the risk of unavailability or unreliability of testing equipment due to preventive or even predictive service measures. Having the relevant spare parts and maintenance kits onsite and maintaining / calibrating devices regularly, will reduce the above mentioned risks significantly. A tailored service level agreement (SLA) ensures that service activities are defined, scheduled and professionally executed. Transform the risk of unplanned downtime into an opportunity of increasing the productivity of your test lab, with the help of AVL Services for Equipment.
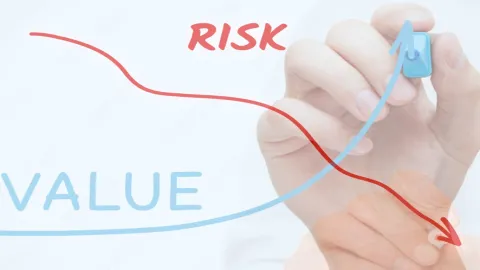
In case a risk turns into an equipment defect, we offer repair either onsite (if technically feasible) or in our repair centers around the globe. Our certified service engineers apply necessary corrective measures, to recover your equipment as soon as possible. The unavailability of necessary measuring equipment can lead to massive problems in your development projects. Therefore we offer possibilities to reduce the overall processing time from picking up the broken equipment until its return, for urgent cases.
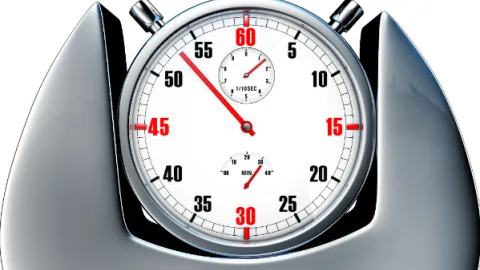