Commercial Hydrogen Engine with 50 % BTE
- Expert Article
CO2 reduction goals for commercial vehicle fleets are pushing the developments of hydrogen engines. Hydrogen as a fuel in internal combustion engines for commercial applications allows either spark ignited lean burn or high-pressure direct injection concepts. Such late cycle direct injection offers benefits in terms of power density and transient response. Also, the fuel efficiency potential is outstanding, a major contributor to optimize total cost of ownership (TCO) for HD (heavy-duty) vehicles.
AVL, Tupy and other partners demonstrated a 50 % BTE on a heavy-duty hydrogen engine using Westport's HPDI (High Pressure Direct Injection) system.
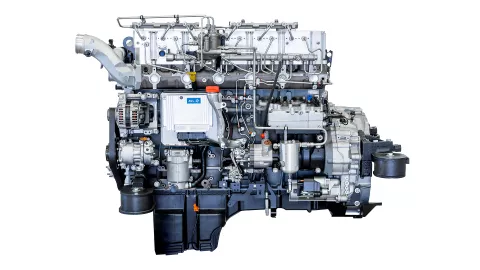
Drivers and Motivation
The European Union has set stringent CO2 reduction targets for heavy commercial vehicles, with new regulations introduced in February 2023. These regulations propose stricter fleet targets starting in 2030 and reconsider the potential of hydrogen internal combustion engines as a key powertrain for Zero-CO2-Emission Vehicles (ZEV). The role of synthetic fuels, such as e-fuels, is still under discussion, with growing political support for their inclusion in the CO2 reduction strategy.
The EU primarily follows a Tank-to-Wheel (TTW) approach, emphasizing non-carbon fuels like hydrogen, though the Well-to-Wheel (WTW) approach may also gain traction in certain markets. In the US, the EPA's March 2023 update aligns with these goals, exempting vehicles using hydrogen from CO2 testing, while California's CARB regulation aims for a zero-emission fleet by 2045, excluding hydrogen engines from the ZEV category.
Hydrogen and its Properties as Fuel for HPDI
We compared fuel properties of hydrogen with diesel and methane, highlighting key considerations for hydrogen's use in engines. Hydrogen's internal mixture formation with direct injection results in a higher mixture calorific value, increasing the excess air ratio for the same air mass flow. It has a much lower minimum ignition energy than other fuels, making it prone to pre-ignition but suitable for late cycle direct injection. The auto-ignition temperature of hydrogen is high, like methane, requiring specific measures to achieve auto-ignition akin to diesel processes. Additionally, hydrogen exhibits wide flammability limits, accommodating both lean and rich mixtures.
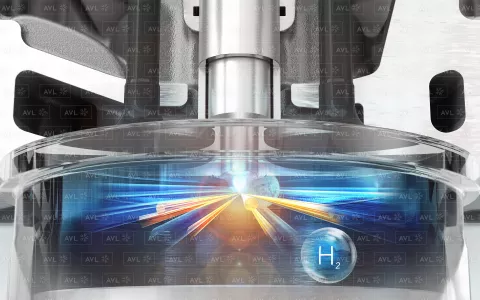
The Demonstrator Program
In a common project of AVL, TUPY, Westport and ITnA (TU-Graz) an H2-HPDI demonstrator was designed, built up and tested. Base engine was a 13L HD multi cylinder diesel engine. The 265 -bar peak cylinder pressure capability (for demonstration purposes) was adequate for high pressure direct injection investigations with focus on maximum achievable BTE. It was equipped with high pressure EGR and a VGT (variable geometry turbine).
The design modification was conducted by AVL. The dual-fuel injectors and the gas (H2) conditioning module from the Westport HPDI 2.0 fuel injection system were considered. Diesel fuel and H2 rail, the fuel pipes and the valve cover were tailored to the demands of base engine and the fuel injection system.
AVL modified its AVL RPEMS (Rapid Prototype Engine Management Systems) for high pressure direct injection operation, which enables transient engine operation.
Efficiency Potential
The baseline diesel engine showed highest brake thermal efficiency (BTE) of 47.6 %. After equipping the base line engine with Westport's HPDI 2.0 fuel injection system, measurements with hydrogen showed a brake thermal efficiency of 49.1 %, which is an increase in brake thermal efficiency of +1.5 %-points. Contributors were the additional expansion work due to the late cycle hydrogen direct injection and a reduced friction due to lower injected diesel quantity and lower injection pressure (between 200 and 350 bar).
An additional optimization of the engine's gas exchange enabled the demonstration of a brake thermal efficiency of 50.1 %.
For further brake thermal efficiency increase an estimation has been conducted based on 1-D simulations and comparable engine measurements. According to the estimation a brake thermal efficiency of 51.7 % could be identified by increasing the compression ratio to 23.1 and installing a high efficiency turbocharger with fixed geometry twin scroll turbine.
CO2 Reduction Potential
The H2-HPDI engine did run on a hydrogen energy ratio of 97.5 % in full load conditions. A liquid pilot has turned out to be the only robust measure to ensure stable and robust conditions for an auto ignition of the hydrogen. Pilot quantities as currently used are low enough to fulfill a potential CO2 limit of 3 g CO2/t.km for HD long haul truck transport.
Summary, Outlook and Risks
A collaborative project by AVL, TUPY, Westport, and ITnA (TU-Graz) developed and tested a hydrogen high-pressure direct injection (H2-HPDI) engine, achieving a brake thermal efficiency (BTE) of over 50 %, with potential improvements up to nearly 52 %. The engine demonstrated performance comparable to diesel engines, with similar full load power and transient torque characteristics.
Fuel efficiency is a major contributor to optimize total cost of ownership for heavy-duty vehicles. Therefore high-pressure direct injection is an enabler to achieve carbon neutrality with highest efficiency for high load operation profiles combined with the robustness needed for commercial vehicle applications.
The H2-HPDI engine operated with a hydrogen energy ratio of 97.5 % at full load, using a small liquid pilot injection to ensure stable auto-ignition. This setup meets potential CO2 emission targets of 3 g CO2/t.km for heavy-duty transport.