The measurement technique is based on the piezoelectric effect, which gives you several advantages such as maximum stiffness, high bandwidth measurement and the fact, that only one transducer covers the entire measurement range without recalibration. The measurement chain consists of the Dynamic Torque Transducer, AVL X-ion™ and AVL IndiCom™ Dynamic Torque Toolbox – this combination utilizes the full potential for your e-motor testing.
Operating principle | Piezoelectric, charge output |
Torque output | Mz |
Force output | Fx, Fy |
Dynamic torque range | +/- 3,500 Nm |
Sensitivity (nominal) | 37 pC/Nm |
Accuracy | < 0.5 % FSO |
Dynamic later force range | +/- 18 kN |
Operating temperature (non-condensing) | -45°C to 150°C |
Max. weight unit under test | 100 kg |
Stiffness | 500,000 kNm/rad |
Clear Differentiation Between Torsional Oscillations and Vibrations
By clearly differentiating these two phenomena the efficiency during the development phase is increased.
Rely on Your Measurement Results
Since the Dynamic Torque Transducer is always installed at the same position on the testbed, you can trust the collected measurement data.
Repeatable and Reproducible
The combination of the fixed installation position and the outstanding accuracy ensure not only repeatable, but also reproducible measurement results during the development phase.
Measurement Results in Newton and Newton-Meter
Receiving the measurement results in N and Nm improves the simulation as the intermediate calculation from acceleration data (mm/s²) is not required anymore.
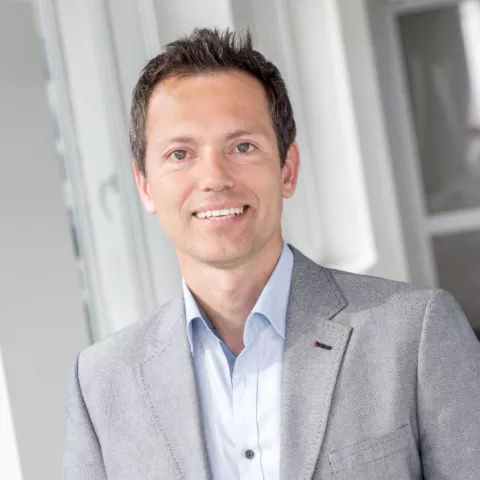
With the Dynamic Torque Transducer you can see all forces and moments of dynamic processes of an electric motor – for optimization, durability, and production assurance.”
– Mario Propst, Principal System Line Manager, AVL List GmbH