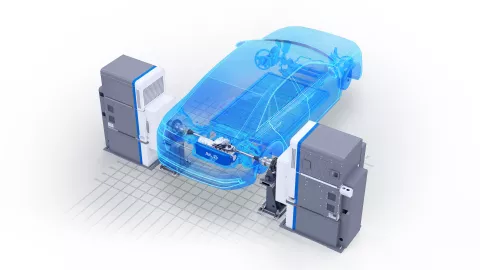
Our dynamic calibration solutions for e-drive and e-axles can be used to shift many development and optimization tasks from vehicle level to component level. This enables you to meet your requirements in terms of performance, cost and flexibility. You can couple component testbeds, such as inverter testbed, e-drive testbed, or e-axle testbed, with real-time dynamic vehicle simulation. The flexibility of this solution allows for the integration of additional models when needed, ensuring that every aspect of the development process is thoroughly examined and optimized.
Scoping Workshop
We discuss and determine the current situation and framework requirements to identify the most suitable solution.
Proof of Concept
We showcase the methodology to demonstrate capabilities and necessary efforts.
Cost Reduction Calculation and TCO Evaluation
We assess the cost and total cost of ownership both with and without the insights gained from the proof-of-concept project to support your make-or-buy decision.
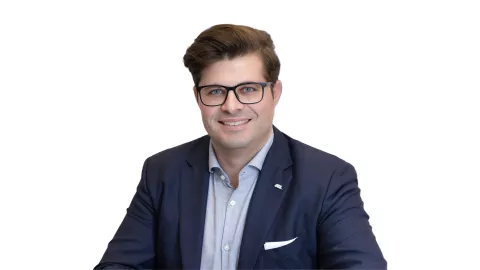
When you combine physical testing and development with real-time simulation, it creates this amazing chance to make better products faster and at a lower cost. It's like killing two birds with one stone!
– Björn Wultsch, Project Manager IODP, AVL