5 Reasons Why PreonLab Is the Ideal Simulation Software for Vehicle Soiling Simulations
- Blog
Siddharth Marathe, Technical Marketing Engineer, FIFTY2 Technology
Understanding and managing the influence of soiling on a vehicle is a critical aspect of driving safety that needs to be considered while designing vehicles. Soiling or contamination can be caused by the deposition of fluid and solid contaminants on the vehicle surface due to splashing, harsh weather conditions while driving, or the accumulation of snow or mud on the vehicle. This can lead to many undesirable issues. There is the possibility of impaired vision for the driver, and reduced visibility of the vehicle or key components of the vehicle such as license plates and lights for other traffic participants. Furthermore, with the advancement in the use of sensors for safety and autonomous driving systems, the deposition of contaminants on these sensors is an area of increasing interest. In fact, with higher level autonomous driving, it is crucial to avoid dirt or too much water on the corresponding sensors and cameras, and having insights that are beneficial to the correct placement of such sensors and cameras is vital.
The extent of soiling depends on many factors related to the driving conditions, the amount of contaminant present, and the aerodynamics of the vehicle. This leads to a myriad of scenarios that need to be considered during physical testing of the vehicles. The use of CFD simulations has proven to be an effective and cost-efficient way to complement such physical testing. Not only is it possible to cover more scenarios as part of virtual testing, but once the simulation tools are validated properly, they can also help make predictions, removing the need to manufacture an entire prototype for every single design iteration. As a result, fluid simulations for vehicle soiling applications have been gaining importance across the industry with every passing year.
While fluid simulation tools can be invaluable in identifying critical errors early in the design stage, they face a different set of challenges, compared to physical testing. Typically, a large amount of time and expertise needs to be invested in generating meshes for conventional numerical methods. The behavior of different fluids on various vehicle surfaces must be properly captured. In order to ensure high simulation accuracy, high simulation resolution is required. This means that the computational effort required can be quite substantial. Furthermore, the aerodynamic effects on the vehicle play a significant part in the soiling pattern and need to be considered in the simulation. Including unsteady airflows in the simulation, which is necessary for accurate droplet behavior, can result in a considerable increase in memory requirements. Collectively, all of this results in increased project turnaround times and costs. Hence, it is imperative to work with fluid simulation software that gives accurate and reliable simulation results, while efficiently reducing the computation time and memory footprint of the simulations. With this in mind, let us take a look at why PreonLab may be particularly well suited to help you overcome the hurdles of vehicle soiling analysis.
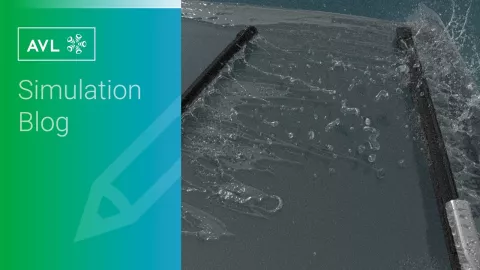
PreonLab is all about particles. It is based on the Smoothed-Particle-Hydrodynamics method, which is a mesh-free, particle-based simulation method. Due to its purely Lagrangian approach, meshing, as is commonly known to users of conventional grid based CFD methods, is not required. As a result, a significant amount of time and effort can be saved during simulation setup. Furthermore, at the core of PreonLab's revolutionary PREON technology is a highly functional implicit solver that enables large time step sizes (CFL 1), fast computation per time step, and spatially adaptive particle resolution without compromising stability. In addition to these inherent performance advantages at the core of the solver, PreonLab has been designed to provide an intuitive user experience, a plethora of easy-to-use features, and multi-platform support across different types of hardware.
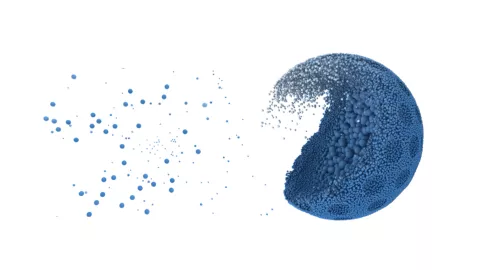
PreonLab can be useful for simulating a variety of soiling applications. The software provides presets for fluids like water and oil, as well as in-built presets for different types of snow, with water and snow being materials of particular interest for soiling simulations. Video 1 shows a collection of some simulation examples with water and snow.
Video 1: Vehicle Soiling Applications – PreonLab
In addition to well established models for adhesion and cohesion, PreonLab provides an additional parameter called Lateral Adhesion to grant more control over droplet behavior. Video 2 shows the effect of the Lateral Adhesion parameter on droplet behavior, and video 3 shows an example of a windshield simulation using this parameter.
Video 2: Impact of the Lateral Adhesion parameter on droplet behavior.
Video 3: Example of a windshield simulation using Lateral Adhesion.
Moreover, it is also possible to define physical properties for additional Newtonian and non-Newtonian fluids and simulate a wider range of user-defined materials. Users can create and store custom presets and have them ready for use whenever required.
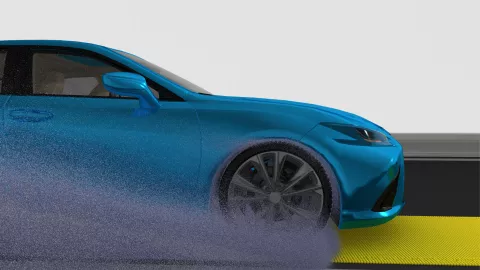
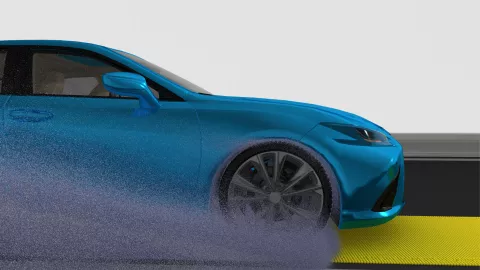
At the core of PreonLab's development is FIFTY2's commitment to providing efficient, high performance simulation software. This includes developing the software to maximize simulation speed while minimizing simulation memory requirements.
Continuous Particle Size (CPS) is a unique, advanced algorithm for spatially adaptive particle refinement and coarsening, which does exactly this. Typically, it is necessary to have high simulation resolution i.e. fine particles in regions where accuracy matters most. In the case of soiling simulations, this could be regions within the wheelhouse of a vehicle, regions along the surface of the vehicle, or around sealing elements through which leakage can occur. It is desirable to have a lower resolution, i.e. coarser particles away from these regions of interest, to keep the total number of particles in the simulation, and thus the simulation time and memory requirements, to a minimum. With CPS , the particles are refined and coarsened for each simulation step in an efficient manner, and it is possible to have large size ratios between the largest and smallest particles in the refinement regions. As a result, there is no need to compromise between simulation accuracy and simulation time and memory to have the best possible simulation performance.
Besides, using CPS in simulations and defining regions of interest is quite straightforward even around complex geometries. The Surface Proximity Refinement feature allows you to define refinement regions based on their proximity to selected solid surfaces. Figure 3 shows an example of surface proximity refinement applied only to the right front wheel of a car.
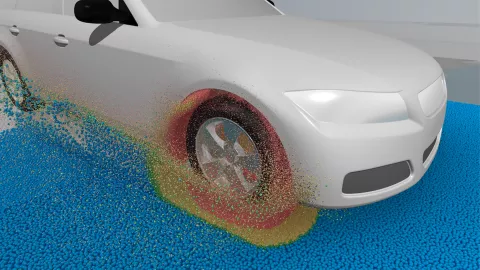
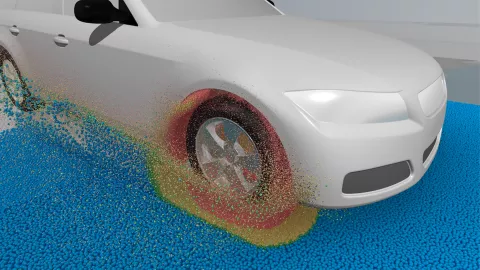
Another important aspect which helps reduce the memory footprint of a simulation is PreonLab’s ability to sample only the required number of solid surfaces in the simulation per simulation step. Dynamic Sampling makes sure that only solid particles that have fluid particles in their vicinity are active during each simulation step. Thus, the total number of active solid particles and consequently, the total memory requirement is kept as low as possible. This can be quite beneficial for soiling simulations, which can include many solid particles that represent all the solid meshes (e.g. vehicle and road geometries).
Figure 4 shows the impact dynamic sampling can have on the number of active solid particles in a car tire splash simulation, like the one seen in figure 2. With dynamic sampling switched on, the simulation reaches a maximum of 83.5 million active solid particles as the fluid spreads due to the splash. On the other hand, with dynamic sampling off, the simulation would sample all possible solid surfaces in the simulation scene, even ones that are further away from the fluid, as particles, leading to a total solid particle count of almost 1 billion from the very first simulation step.
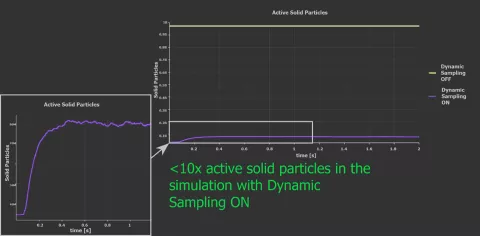
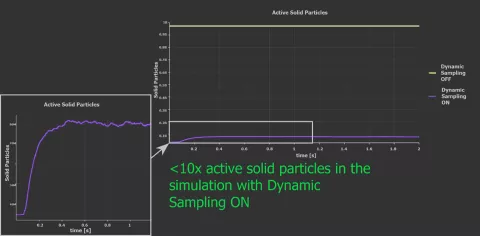
As already mentioned, soiling simulations can be quite challenging in terms of computational cost and memory requirements. This means that the simulation times can be quite long and lead to a substantial increase in project turnaround times.
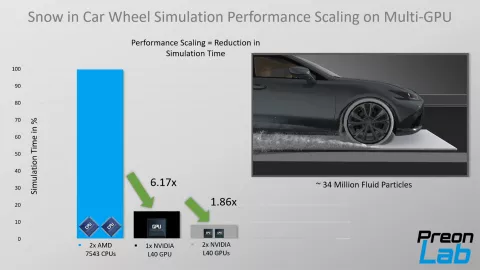
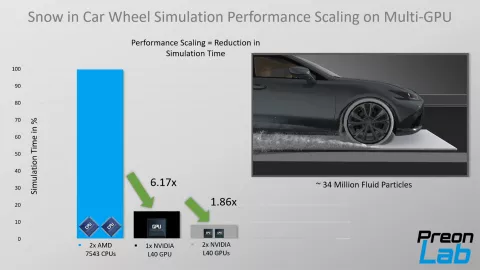
In most cases, GPU-acceleration allows for significantly higher performance per watt compared to traditional simulation on CPUs. Consequently, high-end GPUs also outperform high-end CPUs in terms of simulation runtimes. This can be quite promising to reduce simulation time for soiling simulations. However, while GPUs can help perform simulations within a fraction of the time required on CPU, they do face memory restrictions. Hence, PreonLab 6.1 also offers multi-GPU support which makes it possible to accommodate large simulation scenes across multiple GPU cards and benefit from a further performance boost due to the almost linear performance scaling possible across multiple GPUs.
As one can imagine, this performance and memory boost with multi-GPU is particularly advantageous for soiling simulations. Figure 5 shows the performance boost possible with PreonLab 6.1’s multi-GPU support for a simulation showing the accumulation of snow in the wheelhouse of a car.
Airflow Visualization
As mentioned earlier in this article, the aerodynamics of the vehicle have a significant impact on the soiling pattern. In fact, the inclusion of transient airflows in the simulation is essential, especially for simulations such as those aimed at capturing soiling patterns on the side windows due to A-pillar overflows or on the rear end of the vehicle due to splashing.
PreonLab supports the import of transient as well as steady-state air flows via the CSV format or the EnSight Gold format. The imported airflow can then be simply visualized with the help of a Vector Field Visualizer to ensure correct simulation setup, as can be seen in video 4.
Video 4: Visualization of transient airflow with a Vector Field Visualizer in PreonLab.
Wetting Sensor
The wetting sensor measures the current and total amount of wetting of any solid object it is assigned to. A sensor can be easily connected to any solid mesh in the simulation, with just a couple of clicks. The sensor measures and visualizes where and how much fluid has been or is currently in touch with a solid object. This is an exceptionally handy feature for soiling simulations, as it simplifies the analysis of soiling patterns on vehicle surfaces and identification of critical locations which are prone to contamination or leakage. Figure 6 shows how the soiling pattern caused by a tire splash is visualized with a Wetting Sensor connected to the side of a vehicle.
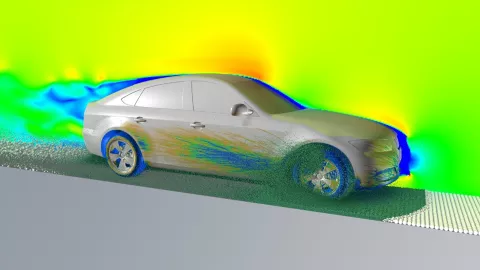
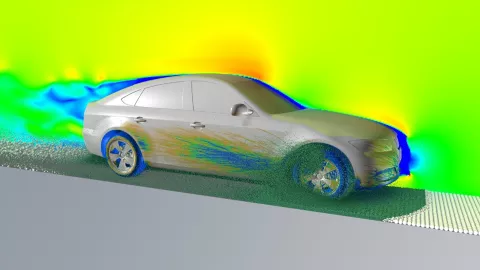
Pathlines Sensor
Pathlines can be very useful when it comes to analyzing the results of soiling simulations. In PreonLab, the feature visualizes the trajectory traveled by a single particle as well as its velocity magnitude over time. The user simply needs to specify a time range and a region in space to select the particles for which trajectories should be drawn. The region can also be defined in terms of its proximity to a particular geometric surface in the simulation. The pathlines can be visualized with arrows that conveniently indicate the direction of particle flow, as shown in video 5.
Video 5: Pathlines visualized with a Pathlines Sensor for selected particles in a snow simulation.
Photo-realistic Rendering
Finally, PreonLab is well equipped with material presets for commonly used fluids and solids, as well as a powerful in-built, ray-tracing-based rendering tool called the PreonRenderer. With just a few clicks, users can create and share impressive images and videos, which help analyze the vehicle designs and soiling patterns better and gain more insights in an intuitive manner.
Vehicle soiling plays a significant role in various safety aspects of driving as well as the placement of sensors and cameras for autonomous driving. There are many factors that affect the soiling pattern on vehicle surfaces, and it is not feasible to consider all possible combinations during physical testing for each prototype. Thanks to PreonLab's ability to simulate a wide range of fluids, combined with a variety of innovative and easy-to-use features, it is possible to gain valuable insights in the early stages of vehicle design and complement physical testing. In addition, PreonLab's mesh-free approach, focus on simulation performance, and multi-platform support can significantly reduce project turnaround times and costs for vehicle soiling simulations.
Click here to watch latest webinar on Vehicle Soiling.
Stay tuned
Don't miss the Simulation blog series. Sign up today and stay informed!
Read More About This Topic
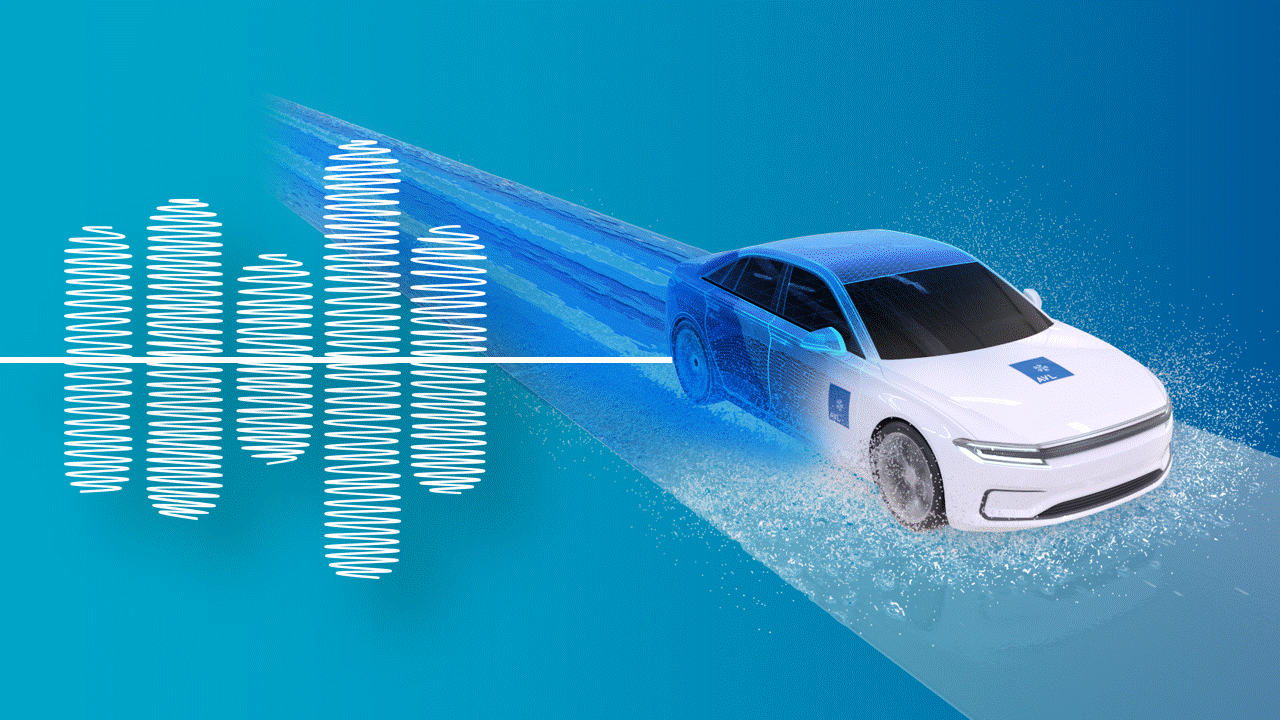
Electric mobility and autonomous driving are changing vehicle design requirements. Water management, vehicle and sensor soiling and aeroacoustics is becoming increasingly important. During our event we will discuss how innovative simulation technologies are accelerating development and optimizing vehicle design.
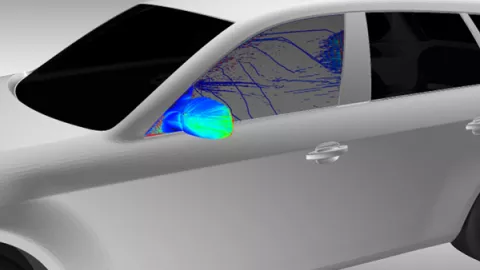
Vehicle soiling phenomena can be a major safety hazard due to obstructed driver’s visibility of the road or abnormal operation of advanced driver assistance systems (ADAS).
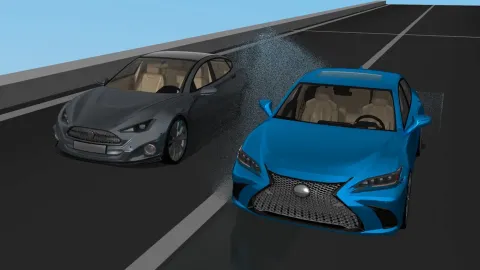
Vehicle and sensor soiling is becoming an increasingly important aspect of vehicle design. The focus is clearly shifting from pure aesthetics to challenges related to safety improvement and cost reduction.
Stay tuned for the Simulation Blog
Don't miss the Simulation blog series. Sign up today and stay informed!