FIRE M has unique preprocessing, solver and post-processing capabilities.
The software can handle any computational mesh, from hexahedral to polyhedral cells, including meshes with arbitrary interfaces. By combining basic finite volume technology for polyhedral meshes with the Immersed Boundary method, you can solve applications with any geometric complexity, as well as body and mesh motions. We call this unique approach the Embedded Body Method.
Solution apps, introduced with Release 2021 R2, provide guided workflows and templates that let you create complex applications in minutes.
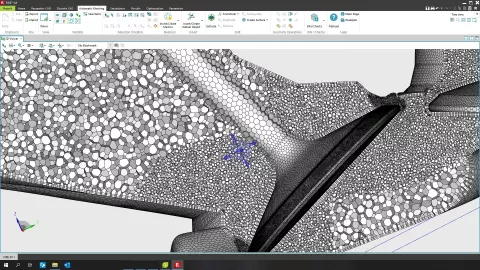
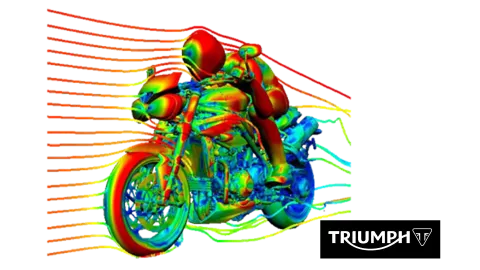
AVL EXCITE™ and AVL FIRE™ M are an integral part of our virtualization strategy, allowing design optimization early in the development cycle. AVL’s simulation solutions help us maintain our position as a manufacturer of class-leading motorcycles.
– Specialist Team Leader, Triumph Motorcycles Ltd.
AVL White Paper – Process-Safe 3D CFD Simulation of Internal Combustion Engines
Download this White Paper and find out how our 3D CFD simulation solution helps engineers realize the ICE’s optimization potential towards zero impact emission and CO2.
AVL White Paper – Reducing GDI Engine Soot Emission by Minimizing Nozzle Tip Wetting
Download our white paper and learn how to reduce GDI engine soot emission by minimizing nozzle tip wetting.
AVL White Paper – Exhaust System Development Through Virtual Prototyping
Download our white paper and find out how we support OEMs in their strive to reduce emissions below the strict legal limits.
AVL White Paper – Using CFD for Quenching Optimization
Download our white paper and learn more about the predictive simulation approach for the optimization of heat treatment processes including air quenching, immersion or water quenching and quenching of steel components.
AVL White Paper – Virtual Fuel Cell Performance and Lifetime Optimization - From Component to Vehicle Level
Download our white paper to find out how AVL eSUITE™ helps OEMs and suppliers get the best performance and longest lifespan from this clean power source.
AVL Customer Case Study - System Simulation in BEV Development at EDAG
For battery electric vehicles (BEV), the high-voltage storage unit is the crucial component in terms of performance, efficiency and range. To optimize these attributes extensive investigations are required. Both in the overall vehicle context and under different, sometimes extreme boundary conditions.
AVL White Paper - Efficient Battery Thermal Management in BEVs
In this paper we present a numerical approach using AVL CRUISE™ M to design a snake shaped cooling channel for cylindrical cells.