Since 2007, we have concentrated on developing safe, cost-efficient, environmentally friendly battery systems with high energy density. Throughout the years, our focus has been on producing top-quality products with a strong emphasis on functional design and innovative production processes. We devise strategies for individual assembly steps and flexible small-batch production of modules and battery systems. The projects listed below represent just a few examples of our extensive work:
- AVL Lighthouse
Our internal project to advance electrification by focusing on battery, EDU, and thermal system development and integration. AVL also leads the integration of E/E systems, control systems, vehicle aerodynamics, and chassis enhancements.
- McLaren Speedtail
Battery pack development project from initial concept to start of production (SOP), incorporating modules into the battery pack for hybrid electric vehicle. The project was executed at the AVL Battery Innovation Center, where small series of battery packs were manufactured.
- LG
Pouch module with a coated aluminum monoframe. Now produced in very large batches and installed in the Audi e-tron and Porsche Taycan, for example.
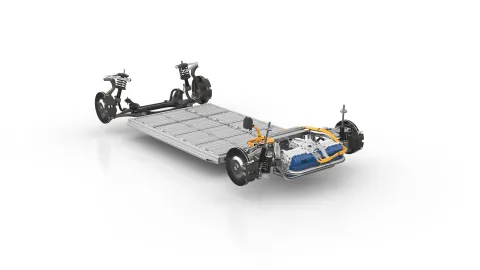
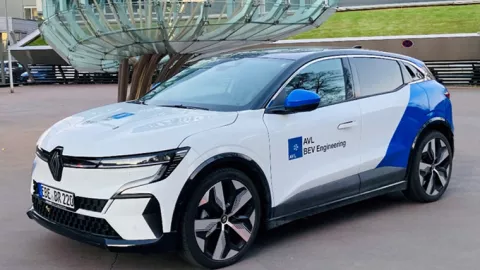
Development methodology
At AVL, we have the expertise, methods, and tools for the entire development process. These include simulation tools and service, virtual testing and validation, creation of prototypes, and integration into the complete vehicle.
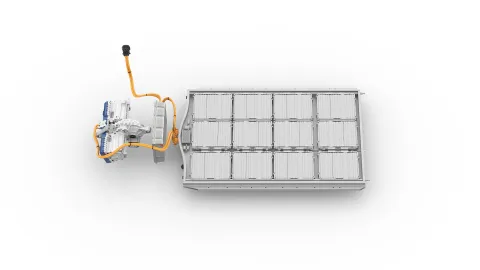
Innovative capability
We have been actively involved in automobile production for more than 75 years, and have optimized our processes for the swift transition from innovation to series-ready products. For batteries in particular, we focus on parallelization of functional and production process development.
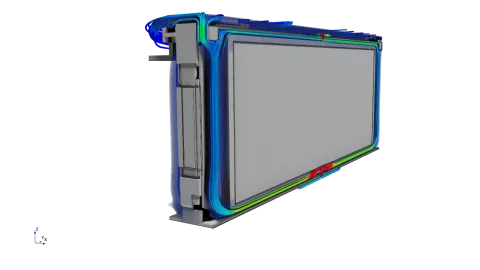
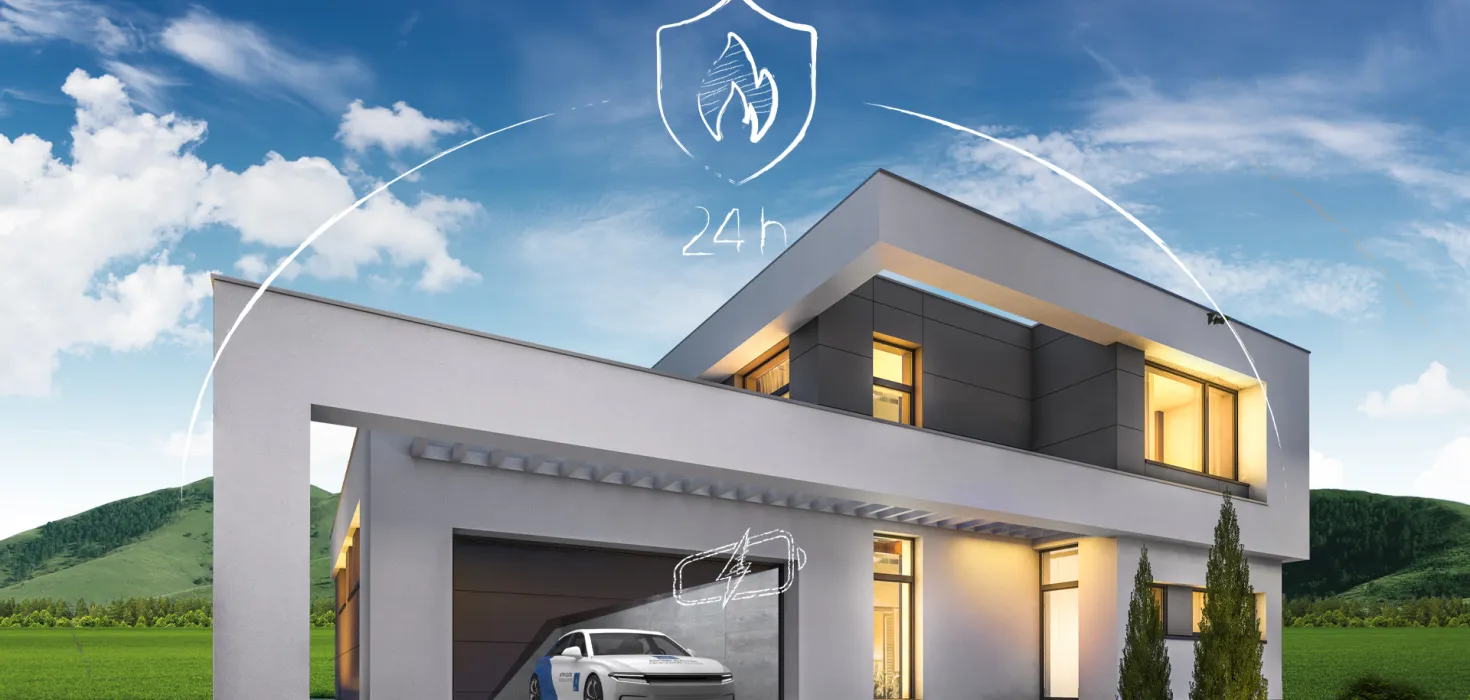
Our innovative battery concepts allow us to reduce CO2 emissions and increase the 24/7 safety of battery-electric vehicles. The key phrase is: no propagation. If a thermal runaway looks likely at cell level, flames must not spread to neighboring cells. Battery design of this type requires a detailed, careful development and verification process. We have developed a unique simulation methodology to realize this swiftly and in a cost-efficient manner. This combines physical tests at cell level with simulations at module and pack level - including the corresponding vehicle interfaces.
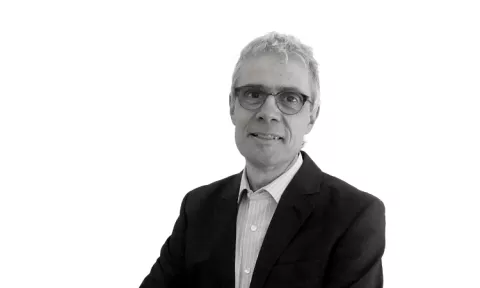
Weight savings, component reductions, easier assembly and service, as well as recycling aspects, all play a key role in the entire battery development process. AVL has already brought solutions with a high level of energy density to market, with low unit and production costs. Our expertise is a decisive advantage for future innovations.
- Volker Hennige, Skill Area Manager Battery at AVL
As an independent service provider, AVL has been a leading battery technology company for nearly two decades.
From the electrode to the pack, we provide complete vehicle integration. We are pioneers, especially with regards to safety, we are already able to realize the no propagation objectives for the next generation of battery electric vehicles.
Our Battery Innovation Center (BIC) in Graz, opened in 2021, added another key future platform to our portfolio, enabling us to provide the best possible support for the automotive industry and its suppliers during the conversion to electromobility. The facility, which covers an area of 1600 square meters, supports all of AVL’s expertise in innovative battery concepts around the world, both in terms of functionality and production process development.
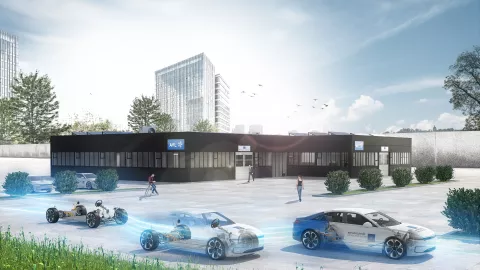
Our global network of engineers and scientists provides the best possible connections for all vehicle disciplines. Wherever you are located – we are able to provide local support.
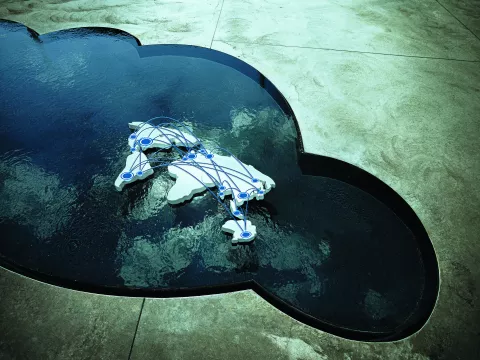
20+
years of experience in battery development
650+
engineers in this segment around the world
900+
executed battery projects
25 %
year-on-year growth in battery development
45
global tech and engineering centers
10+
sucessful series developments
News
Moving steadily into the future: Find out what’s brand new in the field of battery development.