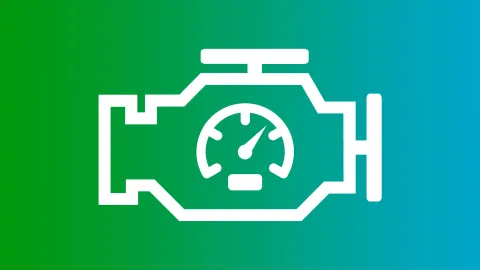
At a glance: The highlights of the simulation solutions in the area of Virtual ICE Development Performance and Emissions.
We are proud to offer you an ESE Diesel Successor in AVL FIRE™ M - very easy to use, fast to set up and execute.
When developing this feature, particular attention was paid to making the setup process of the fully automated segment mesh generation as simple as possible. This significantly reduces the overall complexity of the modeling process, which in turn makes it easy for less experienced users to get started with segment CFD simulations for combustion engines.
The new feature combines the proven tools AVL FAME™ M Engine and AVL FAME™ Poly. It is integrated in the AVL Simulation Desktop and is called AVL FAME™ M Engine S.
The only mandatory inputs required to start the FAME M Engine S process are 2D curves describing the piston geometry and the crank train dimensions. Optionally, you can add a parameterized nozzle tip contour. Furthermore, blow-by and compensation volumes can be activated and will be added automatically to the mesh. FAME M Engine S uses this information to intelligently find the optimal mesh settings for the specified geometry and performs its generation, fully automatically. All required selections are automatically created with this input.
The resulting meshes are polyhedral meshes (consistent with FAME M Engine and the Port Workflow) with identical node distribution on the cyclic boundaries.
They contain local refinements for spray jets and similar features. All FAME M Engine S inputs can be provided as parameters, making it easier than ever to perform case studies.
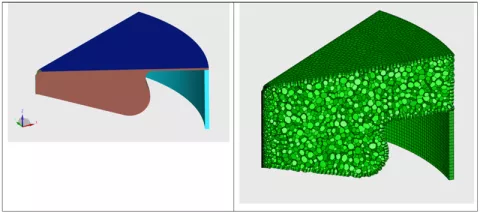
- Multi-Entry Turbine: The turbine component is extended to handle multiple entries and their impact on the turbine
- Restriction / Throttle: This release of AVL CRUISE™ M enables you to model pressure recovery effects in the restriction and throttle components.
- Engine Parameterization Wizard (EPW): The Wizard has been enhanced with new functionality und improved usability
- Gas Dynamic Pipe: The robustness and efficiency of 1D gas dynamics simulations have been improved by introducing a new method to describe momentum conservation at the inlet and outlet face of a pipe.
- Quasi-Propagatory Gas Dynamics Model (QPM): the Quasi-Propagatory Model (QPM) fills the gap between lumped-parameter models and distributed-parameter models, allowing the simulation of propagation effects, even in a compact, lumped parameter framework
- Engineering Enhanced Diesel Cylinder: New models to describe the delivery ratio, the concentration of the residual gas and friction loses have been introduced. The parameterization wizard, which comes with the cylinder model, has been improved to simplify the parameterization of NOx emissions, delivery ratio and the friction model.
- Parameter Masking: This release renders additional User Coding Interface (UCI) parameters from various filter and catalyst input pages applicable to the masking technology
- New multi-component flash boiling model: FIRE M R2022.2 offers a flash boiling model that is applicable to multi-component fuels. This is of particular interest with respect to up-coming emission regulations. Simulation engineers who enhance their models by including multi-component surrogate fuels for spray and engine combustion can now improve accuracy and predictivity. The model addresses various physical processes like fuel nozzle tip wetting, spray plume-plume interaction, spray collapse due to sudden depressurization and other processes, all of which affect engine performance, efficiency and formation of emissions.
- Lagrangian spray now available for Embedded Body-Models: The models related to Lagrangian spray calculations are now able to account for static or moving embedded surfaces within the finite volume computational grid.
- SCR App: This release contains a new solution app for SCR / AdBlue injection simulation as a beta version. The app allows you to define FIRE M single and multi-domain models for standard SCR simulations following the defaults that are also available in the FIRE M SCR templates. It supports both steady state pre-calculation as well as steady state and transient SCR simulation with the standard SCR thermolysis or detailed decomposition model. In addition, the spray nozzle setup, coupled thin wall model, and porosity settings can be used.
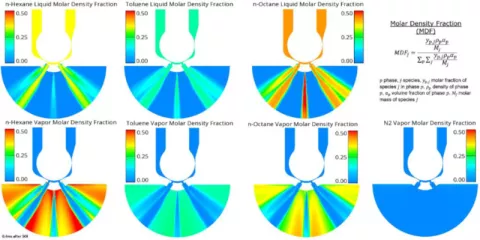