Ammonia – Fuel for the Future
- Blog
Michael Bogensperger, Senior Development Engineer Software
David Schellander, Senior Development Owner
The ever-increasing energy demand of the world's population requires an urgent rethinking of the energy industry with a focus on long-term sustainability. Therefore, in recent years, ammonia has emerged as a potential alternative, parallel to hydrogen, that can be used as a hydrogen carrier and fuel for internal combustion engines. The ECFM-3Z (Extended Coherent Flamelet Model 3 Zones), known as fast and accurate combustion model, has already undergone several improvements in the past to give engineers a powerful tool to simulate combustion of new environmentally friendly fuels. Hence it was only a matter of time that ammonia combustion was implemented in ECFM-3Z.
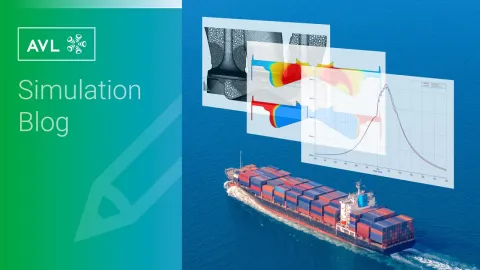
Due to the constant increase in the energy demand of the world population, an urgent reconsideration of the energy economy with the focus on long-term sustainability is increasingly required today. Now this demand is still largely met by fossil fuels, causing global warming as huge negative side effect. A partial or complete switch to a non-carbon-based economy such as hydrogen is proposed. However, a global hydrogen economy is not feasible due to difficulties in storage and transportation. Therefore, in recent years, ammonia has emerged as a potential alternative that can be used as a hydrogen carrier and fuel for internal combustion engines.
Ammonia offers several advantages over pure hydrogen: it has a higher volumetric density, can be liquified at room temperature at pressures of around 10 bar, there is already a widespread global distribution infrastructure because ammonia is already widely used in agriculture (fertilizer production) and in industrial refrigeration. Due to the narrow flammability limit, it is also safer for storage and transportation. However, its use is associated with disadvantages such as toxicity, lower calorific value and slower laminar burning velocity.
The main disadvantage of using ammonia is high NO emissions, which can be treated by catalytic reduction (SCR) in exhaust gas aftertreatment of combustion engines. Efficient combustion engines can run on NH3 in a dual fuel system, either with H2 or diesel as the supporting fuel and jet ignition or with diesel injection ignition as the system to start combustion. In both cases, the load can be controlled by varying the amount of fuel injected, as in the diesel engine.
The ECFM-3Z (Extended Coherent Flamelet Model 3 Zones) has already undergone several improvements in the past. To stay focused on ammonia combustion, the extension for NH3 combustion is briefly described here. The combustion of NH3 to N2 and H2O is exothermic:
4 NH3 + 3 O2 => 2 N2 + 6 H2O
The existing thermal NO mechanism (Zeldovich) is used to consider NO emissions, and the atomic species required for this approach are determined using a chemical equilibrium mechanism.
The newly adapted ECFM-3Z can be used for different combustion systems: pure NH3 spark ignition systems, systems with NH3 ignited by auto-ignition of diesel fuel, but also combinations of systems with NH3/H2/CH4 (or any other hydrocarbon fuel) as the main fuel, which in turn is ignited with diesel.
Ammonia can be used for both spark-ignited (SI) and compression-ignited (CI) engines. For dual-fuel applications, NH3 and additional fuels can be used in SI (hydrogen or gasoline) and in CI (DME or Diesel) engines.
In this study an engine was investigated where the Diesel-ignited ammonia operating concept was considered. This engine served as a good validation case, where several operating conditions were numerically tested, but one (1350 rpm, Lambda=1.9) was used for the calibration of the numerical model setup. For this study an ammonia energy share of 80 % was considered (20 % Diesel, 80 % ammonia). To save computational time, the used engine was performed as a 40°-segment with a structured mesh (see Figure 1).
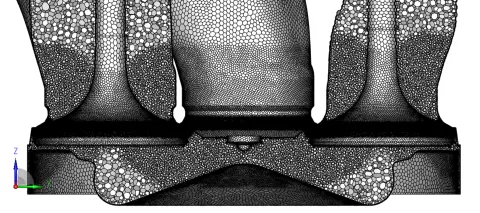
For this operation concept a fuel injection needed to be simulated, where the liquid Diesel injection was simulated using the Lagrangian spray model. Ammonia was available in gaseous form (premixed with air) in the cylinder. After injection, the heat, released by the diesel self-ignition, triggers the combustion of ammonia in the combustion chamber. The complete series of events, injection, ignition and combustion in the engine are shown in the animation in Figure 2.


Figure 3 shows the agreement of the cylinder mean pressure traces obtained from the 3D CFD (AVL FIRE™ M) simulation and the measurement.
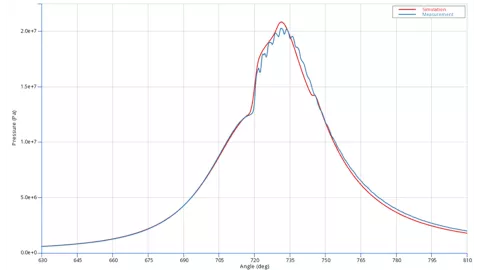
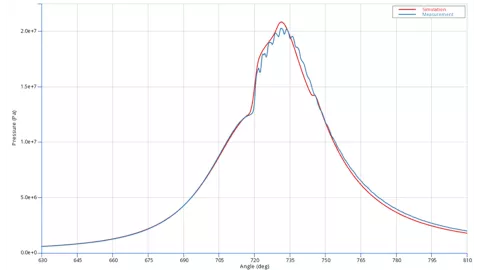
The ECFM-3Z model in FIRE M offers the user the possibility to simulate ammonia combustion quickly, efficiently and robust. The simulation time is comparable to that of conventional gasoline and diesel engine simulations using ECFM-3Z models and way faster than GGPR simulations. The results show good agreement with reference data.
The solution in FIRE M therefore supports all common ignition concepts: spark ignition, micro pilot compression ignition and auto-ignition with external combustion promoters. This makes the new ECFM-3Z model applicable to all ammonia combustion concepts currently under consideration.
Stay tuned
Don't miss the Simulation blog series. Sign up today and stay informed!
Learn More About This Topic
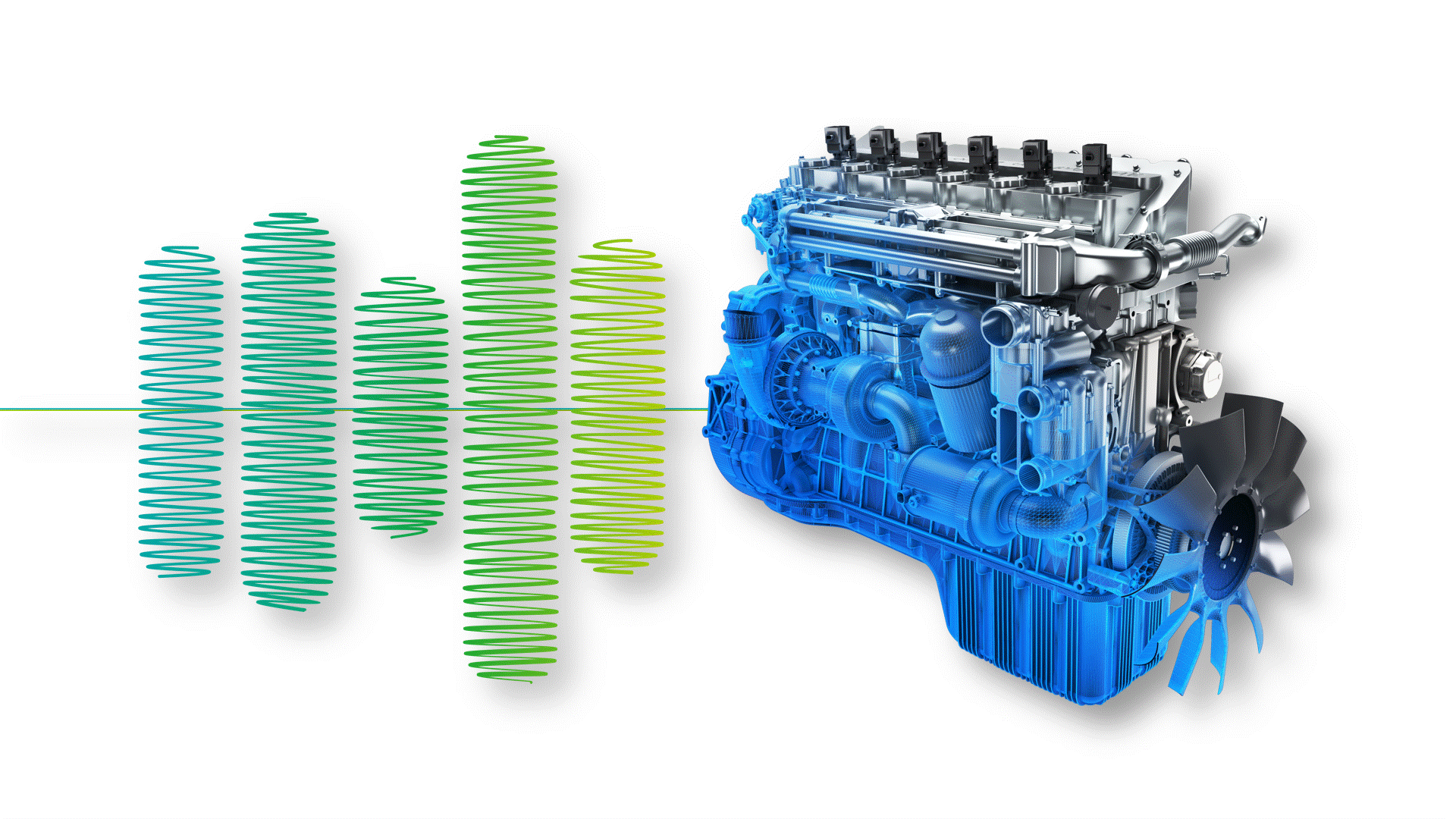
The focus of this part of our event series is on the promising potential of alternative fuels for combustion engines. Green hydrogen and ammonia, for example, enable mobility in sectors that are difficult to electrify and at the same time significantly reduce greenhouse gas and pollutant emissions.
Stay tuned for the Simulation Blog
Don't miss the Simulation blog series. Sign up today and stay informed!